Colloid Mill Machine
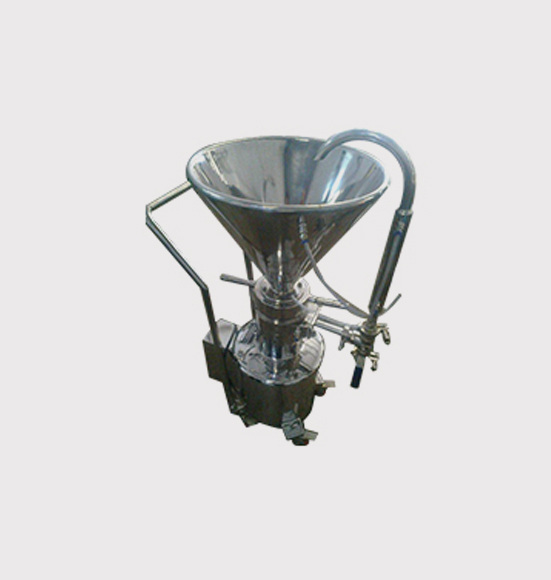
Colloid Mill Machine
Colloid Mill Machine is hugely used for homogenizing emulsifying dispersing, mixing, commuting of liquids to highly viscous products.
We are one of the most trusted firms, engaged of Multi Mill Manufacturer In India, Our Expertise to Exporters & Suppliers of Colloid Mill Machine Manufacturer In India. The Colloid Mill can be used as an in line unit for continuous operation in a process line or with a funnel & circulation line in both horizontal & vertical execution. The working principles of Colloidal Mill are operates successfully for products which must be ground & well dispersed. We are Colloid Mill Machine Manufacturer & it’s used in the Food, Pharmaceutical, and Chemical & Cosmetic Industries and even in Water treatment plants. Colloidal Mill are normally used for Milling, Dispersing, Homogenizing and breaking down of Agglomerates in the manufacture of food paste, emulsions, coatings, ointments, creams, pulps, grease etc.
Description of colloid mill machine:
We are a known Manufacturer, Supplier and Exporter of widely acknowledged Colloid Mill .It is hugely used for homogenizing emulsifying dispersing, mixing, commuting of liquids to highly viscous products. This mill is based on rotor stator principle and it is accessible at most affordable prices in plainand water jacketed (STD & GMP models).
- Our Colloid Mill is manufactured under the supervision of professionals using quality materials.
- Thus, this is extensively applauded and demanded among the masses.
Other Details are as follows:
Operations:
Product is feed to the operating ares of a rotor, having a speed of 3000 R.P.M by specially designed feed device. The product is processed by high sheer, pressure and friction between the stator and rotor, the angular gap becomes narrower towards the discharges section. This processed product continuously leaves the mill through the drain pipe, if required, it can be recirculate.
Salient Features:
- All contact parts are made out of S.S. 304 (S.S. 316 on demand at extra cost). No castings are used to avoid contamination problems.
- Coupling provided between motor shaft and rotor shaft for ease in maintenance.
- Three leak proof neoprene sealing device between the motor and the processing chamber to prevent liquid going in the motor winding.
- Modified design of semi concave teeth in rotor and stator reduces motor h.p. and gives better performance in size reduction without damaging the products.
- Extended bearing housing specially designed to facilitate fine metal contact of rotor and stator. This unique design provides smooth and consistence all around performance and long life of rotor and stator.
- Three way cock system for draining and recirculation of the liquids provided as standard. Extra discharge sprout provided as a standard for viscous products.
- DOL starter with overload relay for protection against single phasing and low voltage.
- Contact parts can be easily dismantled for cleaning
- Special design facilitates adjustments of the grinding gap by exterior screw by means of handle even during operation.
- Flame proof motor and Flame Proof rotary switch can be provided on request at extra cost.