
Ointment Manufacturing Plant
We are engaged in offering well-designed Ointment Manufacturing Plant to the customers. Our Ointment Manufacturing Plant has robust construction and high strength. We employ high grade components for the manufacturing of our Ointment Manufacturing Plant. The Ointment Manufacturing Plant is tested on different parameters by experts. Our Ointment Manufacturing Plants have reliable performance.
The Ointment manufacturing Plant is designed to cater the following process needs
Through – homogeneous Mixing of wax phase & aqueous phase material in Ointment Manufacturing Vessel by means specially designed W shaped anchor
Wax phase vessel for malting of Wax & Oil base
Water Phase vessel for aqueous phase material processing
Inline high speed emulsifier for proper emulsification for finer particle size , better skin penetratation
Charging Hopper to charge Active Ingredients for Ointment Manufacturing Vessel
Ointment / Cream storage vessels – Jacketed/ non Jacketed
Vacuum Transfer of water & wax phases into Ointment manufacturing Vessel
Transfer pumps for transferring finished product into Batch Storage/Staging Vessel
Transfer pumps to transfer product to filling station etc.
Ergonomic anti skid Working platform for fatigue Free plant operation & minimal operator movements
Salient Features
The Drive being from bottom , the machine becomes accessible with the Top Dish opening with a swing out arrangement & hennse enavle for easy cleaning for every change over
No hydraulic lift for top dish opening , hense purely GMP
W shaped anchor ensures SEMI CONTRA motion for better & fast mixing. Even Phase reversals possible. The special blade design ensures a unique flow pattern. i.e. material movement from core to circumferential & upward to downward & vice versa.The Teflon scrappers bolted to baffles & anchor ensures 100 & cleaning , hense no local heating , no charring of product
Duble cartridge type mechanical seal for main manufacturing Vessel ensures vacuum tightness to attain Max vacuum level upto 700 MM of Hg
The inline type Homogeniser ( IKA-WERK type Design 0= ensures 100% recirculation of the product & with the use of specific size sieves , the globule size of the finished products can be controlled
The drive from bottom , hense no spillage of oil , grease & dirt into the product ensures contamination free processing
Un Touched product transfer maintaning highest level of operational hygeine
Ergonomicaly designed anti skid working platform with safety railing for better & safe operational movements
Load Cells for batch weighing avoiding human error
Flow meter for accurate quantity monitoring
Pneumatically aided automatic balves for all process lines & utility lines controlled through PLC
SCADA ( supervisory control & data Aqusition system) base IPC Plus PLC operated control station compatabile with USFDA / EUFDA / GAMP norms
Total documentation support start from Design Qualification to Performance qualification
The team of qualified engineers ever prompt after sales service
Specifications
Model | Working Capacity | Vollume OMV. | Power Cons. | Steam Consumption | Machine Dimension (mm) | ||
(Kg/Batch) | Litres | (HP) | Steam | L | W | H | |
OMP-50 | 50 | 60 | 5 | 100 Kg/Hr | 3000 | 2000 | 2500 |
OMP-100 | 100 | 120 | 9 | 150 Kg/Hr | 4000 | 2000 | 2500 |
OMP-250 | 250 | 300 | 14 | 200 Kg/Hr | 5000 | 2000 | 3000 |
OMP-500 | 500 | 600 | 19 | 400 Kg/Hr | 6000 | 3000 | 3000 |
OMP-750 | 750 | 900 | 24 | 500 Kg/Hr | 7000 | 4000 | 3000 |
OMP-1000 | 1000 | 1200 | 31 | 650 Kg/Hr | 7500 | 5000 | 3500 |
Scada Screen for Bottom Entry Plant
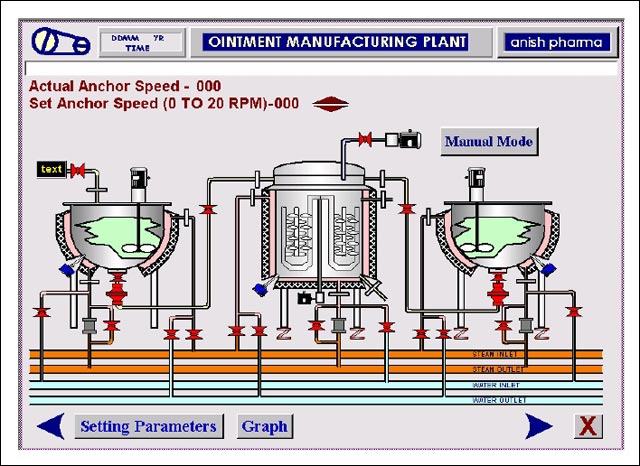