VSI Crusher
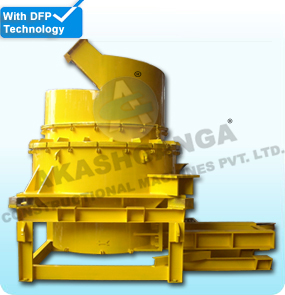
Layout of sand manufacturing plant is similar to Stone crushing plant. It consist of Feeding hopper, Rotopactor, Sand Screen, conveyors / elevators, electrical prime movers and controls, etc. For manufacturing Sand at large scale it is manufactured directly from bigger size stones up to 500 mm size. The feed size of VSI Crusher can be 0 to 40mm. The stone metal of 20mm size can be produced from this feed size. Therefore bigger size stone must be crushed to minus 40mm for feeding in the VSI Crusher. For making sand, for getting more efficiency and less wear the feed size should not be more 15mm.
Specially Designed VSI Crusher for High Silica Minerals Is Our Specialty. This Machine Can Crush Quartz, Quartzite, Glass, Sodium Falspar and High Silica Minerals Very Efficiently With Less Wear Cost.
Small machines can be used along with Stone crusher units, Where Grit and fine particles are waste. With Two crushers a 15 ton per hour capacity machine can be installed.
Generally, 20mm metal and sand has more demand. Material below 12mm doesn’t have any demand. Hence, converting this material into sand is more profitable. VSI Crusher available with us are in range of 30 tons per hour to 250 tons per hour. Same way Artificial sand Making Machine is available in the range from 5 tons to 200 tons per hour. Similarly, Plaster Sand Making Machine is also available from 15 tons to 100 tons per hour.
VSI Crusher & Rotopactor are specially designed machine for manufacturing of cubical metal. Sand Making machine is used for manufacturing Artificial sand. The crushing principal in VSI Crusher, Rotopactor and Sand Making Machine is same. These machines consist of a rotor which revolves a high speed and throws stone particle at vigorous velocity. These stone particles collides on anvil or autogenous stone lining in crushing chamber. The stone particles having kinetic energy when it strikes on crushing chamber brakes into small cubical particles. Crushed particles comes out from the outlet at the bottom of the machine.
The designs of the Rotor of these machines are very special. The wear parts of these rotors are made from highly abrasive resistance material. Autogenious Stone Lining is form as per the locus of stone moving in the rotor. This arrangement avoids the contact of stone particles with soft material of the rotor. On all points where such contact is unavoidable a hard material lining is made. The body of the rotor is covered with armour plates to reduce wear. This way maximum possible wear life of the rotor is achieved. In the design of the rotor high technology and dynamical calculations are done by our highly skilled persons. All such parts are patented to protect intellectual properties. This makes our machine very unique. Due to this special design made using the most modern technology performance of our machine is unbeatable. This is the reason we are pioneer and leader in the market of Sand Making Machine.
Bearings and the Lubrication system is a very important part of VSI Crusher. We have adopted oil Lubrication system which is very critical and difficult to achieve. With the use of high technology and thorough knowledge of designing, we have achieved this system very successfully. The main shape of the machine revolves at many high RPM. It is not so easy to avoid leakage of lubricating oil. Our highly skilled and specialized design engineers made a very successful design and achieved successful oil lubrication system. All other manufacturers uses only grease lubrication system. It will not be a boost to say in the whole world Akashganga’s VSI Crushers and Sand Making Machines are Oil Lubricated.
Due to adoption of Oil Lubrication system we had achieved so many benefits. It is common factor when such a heavy duty machine is running at a very high speed. Heat generation is unavoidable. If the temperature of bearings increases above certain level may damage it. With Oil Lubrication system positive Lubrication is achieved. In this system, we have made cool oil to be circulated in the bearing housing and hot oil is take out. Heat generated in the system is extracted by the lube oil. Hot oil is processed in Heat exchanger and is cooled. While cooling oil is also filtered which keep the bearings clean and cool. This all arrangements increases the bearing life and efficiency of the machine. One more big advantage of this system is the whole rotating body is kept floating which reduces the friction losses. Hence, machine becomes more efficient. The saving due to design criteria of our machine may not be noticeable still there is 3.5% saving in power charges.
The design of this machine is very users friendly. The maintenance of this machine is very easy. Any unskilled person with average brilliancy can maintain this machine. The design of this machine is full proof and very easy. All parts are very ergonomically designed which avoids any miss fitment. All safety measures are automatically inter connected. If there is any deviation in the system machine will not be started. There will be indication on the panel board regarding the fault. The operator can easily understand the same and take corrective action. If all instruction followed seriously machine can run round the clock without any trouble.
The sand produced from our machine strictly satisfy the IS Standard 383 and IS Standard 1542 for Plaster Sand. Just inspecting the sand by bare eyes nobody can judge its fineness modules. Fineness Modules can be tested in testing laboratory. Therefore, any person wants to install sand manufacturing plant before selecting the make of the machine, one must takes some samples of sand from all types of machines manufactured by different manufacturers and get is tested from testing laboratories. Which sample or customer should approve the machine whose sample satisfy the criteria as per IS Standards. Cost of the machinery will be the 2nd preference, 3rd after sales service, 4th will be wear cost. Before selecting the machine all customers must follow the above instructions.