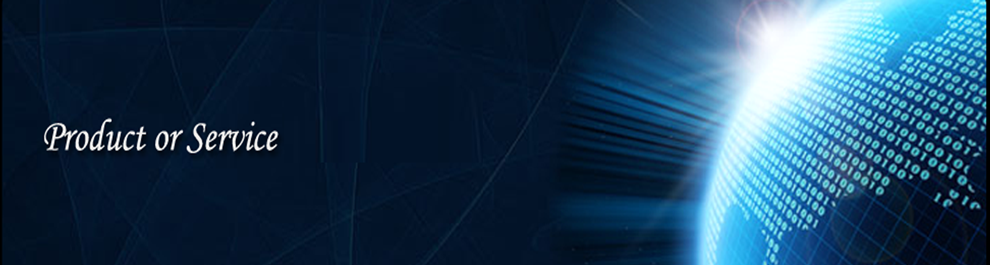
Our Products - Prototypes & Small Batches
Based on the files provided by our customers we map and understand their needs and the manufacturing processes are chalked out using 3D CAD data of the casting requested. Catia as well as Pro/Engineer are some of the tools used for the mould design. Our technicians and employees with their core expertise in CAD can generate the data required for development of cores and segments needed for the moulds.
We have on board 8 expert CAD technicians who are involved in communicating with the clients on consistent basis and this allows for generation of the initial solid model. Subsequent machining takes place through addition of machining stock. By adding of gating as well as feeding systems the actual mould design is started. After splitting the mould and separating the cores, addition of core prints takes place and mould segments as well as cores are located with the interlocks. Following this checking of the mould assembly is done for interference and fit. Interfaces we use include STEP & IGES file formats.
The aim while designing a product is not just to have a lightweight design but one that is efficient as well as economical. Simulation helps in identifying the proverbial chinks in the armour by determining ways in which the products can be made more efficient. Our team of designers along with our cutting edge technology can tackle the challenges head on.
Simulation is the key to the quality of the products developed. The tools used for simulation include -
√ Delcam Power-mill used for machining: Through this simulation machining processes are optimised so as to ensure that errors do not occur when the castings are put through the machining. Power-mill helps in identifying faults in drawings, wrong CNC programs, wrong tools or tool paths and collisions in motion.
√ AutoCast-X used for mould filling and the solidification simulation required for casting process: This helps in improving the casting quality as well as predicting the material properties. This crucial tool helps in mapping of the production processes.
Ascent Cast Tech Pvt. Ltd. has highly effective in house foundry that can deliver components within specified time limits to the customers. The induction furnace has a capacity of up to 150 kg allowing for quick processing and timely completion of several different projects at one time. The castings are shaken after pouring and cooling and are then cleaned. After removal of gating as well as feeding systems, the castings are ready to be heat treated and inspected.
√ CNC Pattern Making -For pattern making needs we first modify the 3D CAD data to meet the pattern making requirements. For tradition patterns parting lines are determine d and the draft angles as well as fillets are added.
√ Laser Sintering
The aim while designing a product is not just to have a lightweight design but one that is efficient as well as economical. Simulation helps in identifying the proverbial chinks in the armour by determining ways in which the products can be made more efficient. Our team of designers along with our cutting edge technology can tackle the challenges head on.
Simulation is the key to the quality of the products developed. The tools used for simulation include:
√ Delcam Power-mill used for machining: Through this simulation machining processes are optimised so as to ensure that errors do not occur when the castings are put through the machining. Power-mill helps in identifying faults in drawings, wrong CNC programs, wrong tools or tool paths and collisions in motion.
√ AutoCast-X used for mould filling and the solidification simulation required for casting process: This helps in improving the casting quality as well as predicting the material properties. This crucial tool helps in mapping of the production processes.
√ Furnace Capacity
• Induction Furnace
« 150Kg
« 50Kg
• Moulding
« Omega 3T/Hr Continues Mixer
« Sand Reclamation 1Ton/Hr
• Lab
« Metal Power Spectrometer
« Image Analyzer
√ Heat treatment
√ Raw Part Inspection
« Spectrometer
« X-Ray Examination
« Hardness Testing
√ Metallographic
√ Dye Fenetration Inspection
• Quality Control Equipment
« Surface Plate 1800mmx 1200mm
« Vernier Height Gauge 600mm
« Vernier Caliper 0 –300
« Vernier Caliper 0-150
« Outside Micrometer 0- 25, 0-50, 50-150
« Out Side Micrometer 0- 50
« Portable CMM Faro Gauge Plus
Final machining is a crucial part of the processes provided by Ascent Cast Tech Pvt. Ltd. Following this crucial process the components can be tested and used. For prototypes greater machining effort as well as care is required.
Testing is a crucial process that follows the completion stage. Prototypes manufactured in-house help to check the efficiency of the products. Bench tests are conducted for validation based on the requirements.
√ Aluminum √ Grey Cast Iron √ SG Iron √ Steel