Tooling for Bearing Industries
Carbide Shoe and Grinding positioning bush
Clamping plates are used for holding the races against the Driving plate during the grinding of Inner and Outer races during Grinding and Lapping.
Prior to external /internal grinding of bearing rings, these rings are normally facing ground on both sides on a duplex grinder with a high level of precision and accuracy for face parallelism and face waviness. One of the faces of the bearing ring is resting on the bevelled edge of the†Driving Plate â€. The other face of the bearing ring is clamped by †Clamping Plate †. The movement of clamping plate is by means of a high precision bearing unit of which clamping plate is one.
Due to this demanding requirement, the†Clamping plate †is normally made of solid one piece sintered carbide of wear resistant grade . The end face of the clamping plate is precision ground and finally lapped to a very high level of surface finish and geometrical accuracy.
Thus a good quality†Clamping Plate†ia VITAL part in the hard machining process of bearing rings.
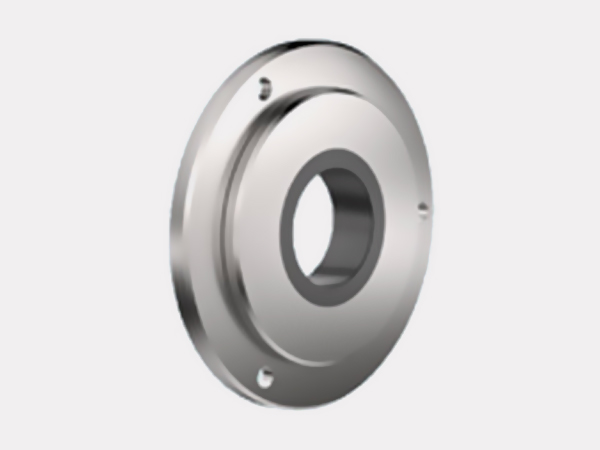
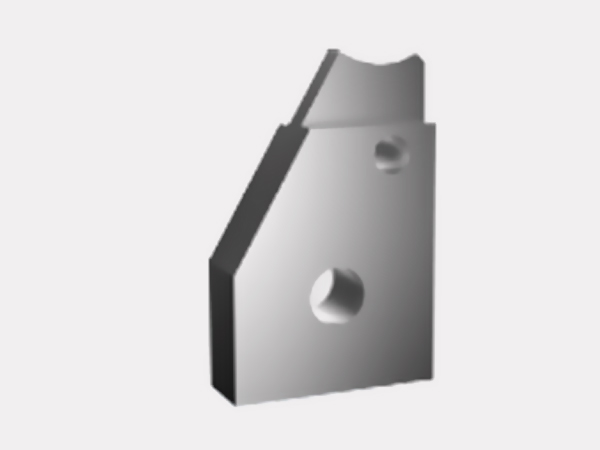
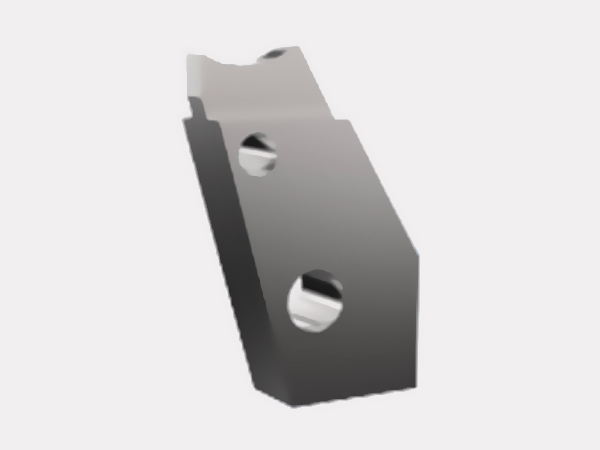
Driving / Backing plates for bearing
Driving plates are used for driving the Inner and the outer races during the Grinding and Lapping operation.
Prior to external /internal grinding of bearing rings, these rings are normally facing ground on both sides on a duplex grinder with a high level of precision and accuracy for face parallelism and face waviness. One of the faces of the bearing ring is resting on the bevelled edge of the †Driving Plate â€. Hence this becomes a †Reference face †for all subsequent hard machining operations.
Due to this demanding requirement, the †Driving plate †is made of composite construction viz: a wear resistant carbide ring strongly brazed to a carbon steel body. The end face of the carbide ring is precision ground and finally lapped a very high level of surface finish and geometrical accuracy.
On the machine, †Driving plate †is fixed to the work head spindle and it is a rotating part.On the machine, †Driving plate †is fixed to the work head spindle and it is a rotating part.
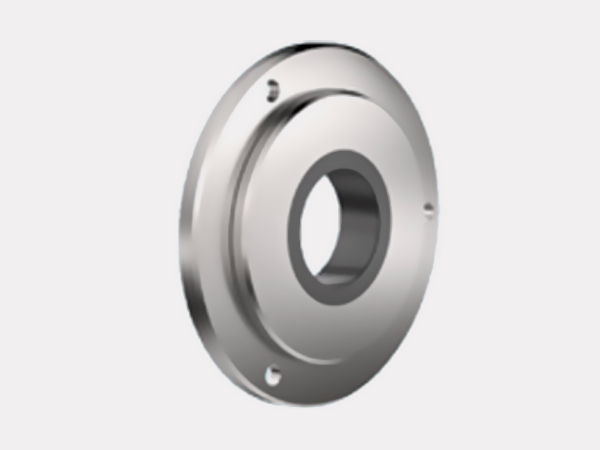
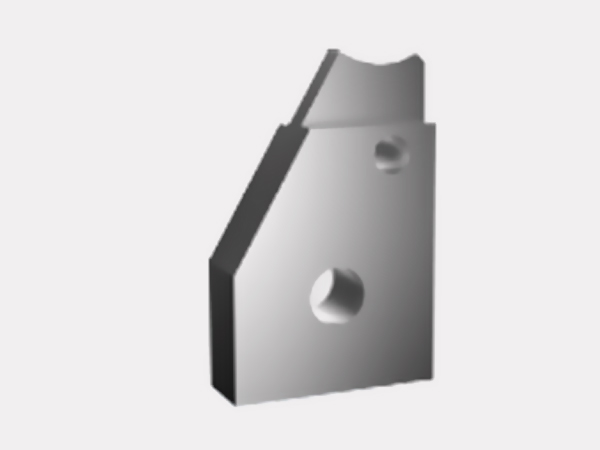
