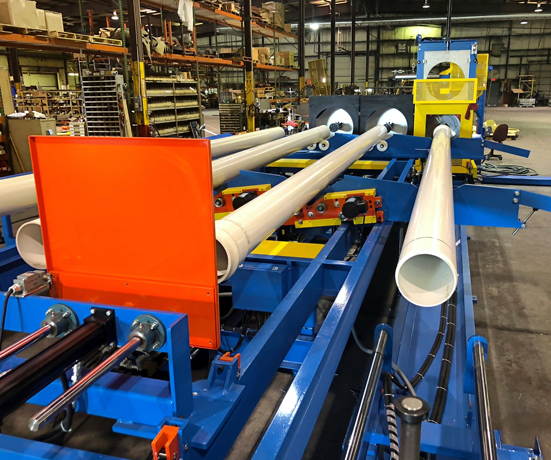
Plastic Extrusion Service
Plastics are everywhere because of their versatility, longevity, and simpler manufacturing requirements. Plastic extrusion, along with injection molding, is one of the most common processes for high-volume production. Generally, extrusion is common for continuous profiles that use pipes, tubes, door profiles, and other bulky items.
Industrial applications of plastic extrusion started over a century ago and continued to advance with time. Even today, it is the go-to method for many plastic manufacturing projects because its simple, efficient, and delivers accurate results.
The following text takes a look at the basics of the plastic extrusion process. Its advantages, limitations, types, and finally the common applications across different industries.
How Does Plastic Extrusion Work?
The plastic extrusion process begins with filling the hopper with smaller plastic pieces that are simpler to process. The feed throat uses gravity to transfer that plastic to the barrel for further processing.
When the material enters the barrel, it starts to be warmed by means of at least three intensity zones, where the temperature intensity increases as you move away from the feed throat. As the temperature increases, the barrel uses a continuously rotating screw to push the molten plastic towards the next component of the machine. The screw and pressure additionally create heat, so the intensity zones themselves don’t need to be basically as hot as the expected extrusion temperature, thereby saving energy and facilitating the extrusion process.
The liquid plastic leaves the barrel through a screen supported by the breaker plate. This screen eliminates foreign substances from the material and maintains the internal pressure. The material goes through a feed pipe into the uniquely fabricated die, which has the same shape as the extrusion profile you want from the project. At the point when constrained through the die, the molten material creates the same shape as the die opening, which completes the extrusion process.
When completely through the die, the extrusion profile is cooled in a water shower or by means of a bunch of cooling rolls to ensure that the shape of your thermoplastic extrusion profile becomes permanent.