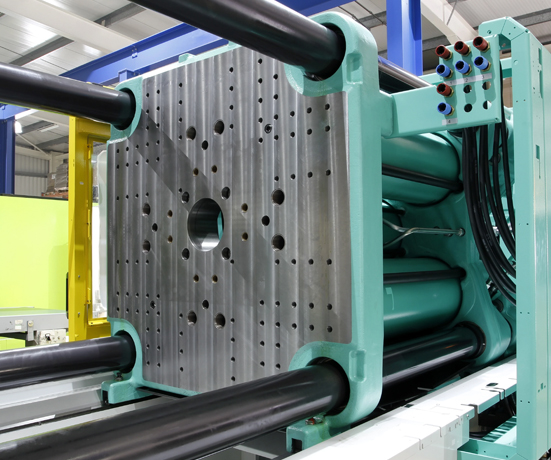
Plastic Injection Moulding
Plastic Injection moulding is a widely used manufacturing process to produce plastic components due to its affordability, effectiveness, and high reliability. Injection Moulding (IM) is a manufacturing process in which a polymer is heated to a highly molten state and forced to flow under high pressure into a mould. The molten plastic then cools and solidifies inside the desired part-shaped cavity. Finally, the moulded part, known typically as moulding, is extracted from the mould.
Plastics and elastomers are the most common moulded material, and manufacturers produce large quantities of mouldings. Similar to metal casting and 3D Printing, IM can produce distinctive near-net shape parts with complex and intricate shapes.
Although larger parts could take 60 seconds or longer, the typical production cycle time is between 10 and 30 seconds. Also, the mould can contain more than one cavity, so multiple mouldings are produced each cycle.
Because it produces plastic mouldings in large quantities at a meagre cost per unit, injection moulding is extremely common. Two advantages of injection moulding are its high repeatability and substantial design flexibility. However, economic factors are typically the primary constraint on injection moulding because of the high initial mould investment needed. The turnaround time for initial production is also very long.