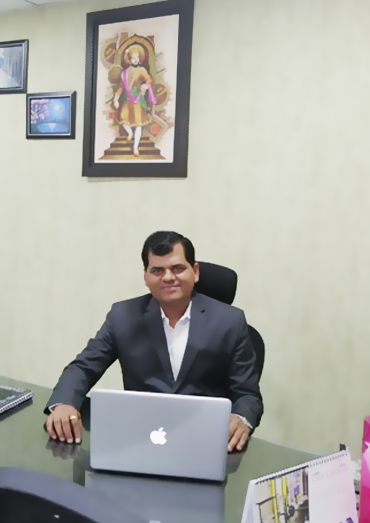
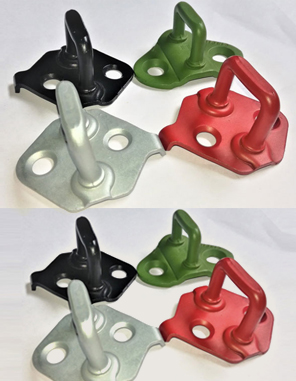
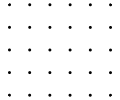
Elixir Industries is an ISO 9001:2015 certified company, being “A highly quality obsessed & Reliable”
precision machined, cold forged components manufacturing source shall be the best strategic business partner for your highly esteemed organization. Company was incorporated by young minds in year 2006 with sole purpose of supporting customer needs.
Currently company is run by partners carrying combined engineering techno-commercial experience of 34 Years in Product development, Vendor development and SCM activity in Automotive, Oil and Gas and FMCG.
We provides an end-to-end solution taking ideas and concepts and making it into a finished product. Our forte is into application development & we continuously keep ourselves abreast of latest technological developments that customers always look for. We are a well known entity, engaged in manufacturer & supplier of a wide range of cold forged components. Our offered range is manufactured at the vendor's end with utmost precision using latest technology according to market trends. The entire range of our product is highly praised by our esteemed clients for its stylish design. Our highly qualified professionals manufactured our entire range using fine quality raw material and cutting edge technology.
Our Group Of Companies
- ELIXIR INDUSTRIES UNIT-I, AHMEDNAGAR
Manufacturing cold forged , sheet metal and precision machining parts. - ELIXIR INDUSTRIES UNIT-II , PUNE
Manufacturing of highly Precision machining parts. - TECHNOCOAT SERVICES, PUNE ( 2014)
Aluminum zinc Flake coating , Xylan coating and Phospheting plant.
Organic capabilities :
1. Xylan coating and testing :
- Xylan is generally used to reduce friction, improve wear resistance, and for non-stick applications. Additionally, it can be used to protect a metal from corrosion. The most commonly known application is in non-stick cookware but Xylan coatings have also been used extensively in the automotive industry and for corrosion protection in the oil and gas industry.
- Xylan is the umbrella trademark for most of the Whitford Corporation fluoropolymer coatings line. Xylan is made of low friction, wear resistant composites of fluoropolymers and reinforcing binder resins. Xylan coatings can be one-, two- (primer and top-coat), and three- (primer, mid-coat, top-coat) coat conventional and reinforced (filled) coating systems
2. Zinc phosphating and testing :
- Zinc Phosphate Coating Services is applied when increased corrosion resistance is required. Zinc phosphate withstands 240 hours of neutral salt test.A wide range of coating weights may be obtained: from very thin fine crystal films to heavy deposits with weight up to 4 g/ft2 (40 g/m2).
- The coating color is gray of different tins: from light to dark. Finer zinc phosphate crystals produce darker color. Dark gray color is also characteristic for the high carbon steel substrates.
- Zinc phosphate coatings may be applied by using immersion or spray technique.
- Light and medium weight zinc coatings do not require substrate surface activation. The substrate surface should be acid activated prior to heavy coating deposition. Zinc phosphate is used not only for non-coated Steels and cast irons but also for galvanized (zinc plated) steel parts.
3. Induction heat treatment
- In modern manufacturing processes, this form of heat treatment offers a beneficial combination of speed, consistency and control. Although the basic principles are well known, modern advances in solid state technology have made the process remarkably simple, cost-effective heating method for applications which involve joining, treating, heating and materials testing.
4. Aluminium zinc flake coating and testing
- Zinc flake coating is a zinc-aluminium paint based coating which provides high corrosion protection and is replacement for hot-dip galvanizing for smaller /threaded components which require thinner and good asthetic coatings with higher life.
5. Shot blasting
- Shot blasting process carried out to prevent metal fatigue or cracking as well as for cleaning and surface hardening. In this method, the role of the shot is to remove impurities, rust, scattered pieces of rubbish or remains that may affect metal strength. It is environment friendly and a rapid, cost effective surface finishing method which is used for cleaning, polishing metal and other surface by applying high speed stream of shots.
6. Brass/Silver brazing
- Brazing is a metal-joining process in which two or more metal items are joined together by melting and flowing a filler metal into the joint, the filler metal having a lower melting point than the adjoining metal. Brazing differs from welding in that it does not involve melting the work pieces and from soldering in using higher temperatures for a similar process, while also requiring much more closely fitted parts than when soldering. The filler metal flows into the gap between close-fitting parts by capillary action.
Inorganic Capabilities :
- Approved raw material provider
- Third party material testing laboratory
- Customer Approved Heat Treatment Supplier