Servo Drives
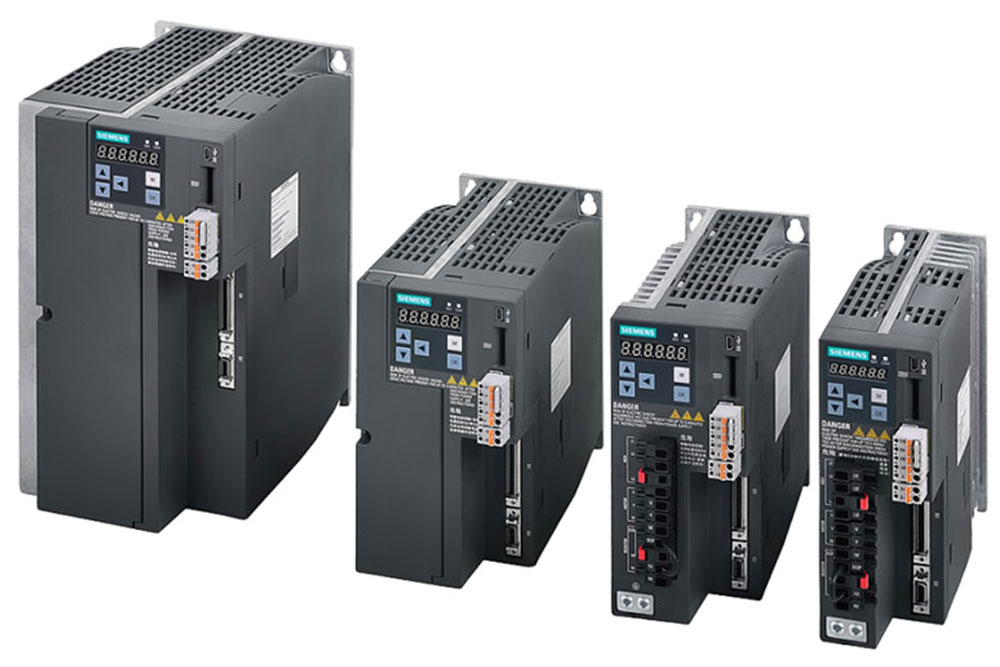
V90 Drive
The servo drive system comprises the basic SINAMICS V90 servo converter and SIMOTICS S-1FL6 servomotor. The system features eight converter frame sizes and seven motor shaft heights to cover a performance range from 0.05 kW to 7.0 kW for operation in single-phase and three-phase networks. Can be simply integrated via PTI, PROFINET, USS, Modbus RTU. The SINAMICS V90 servo drive system enables a wide range of simple Motion Control tasks to be implemented cost-efficiently and conveniently with the focus being on dynamic motion and processing.
SINAMICS V90 Servo Drive System – An Overview of its Strengths
S110 Drive
The SINAMICS S110 with its built-in basic positioning system is ideal when you need to position machines axes simply, quickly, and accurately. While the positioning drive relieves the higher-level machine control system of the task, this flexible drive actually offers much more. As an alternative to a basic positioning system, the drive can be assigned set values of speed or position using analog input or a field bus interface, such as PROFIBUS, CAN, PROFINET. Additionally, the positioning drive can control a wide range of built-in safety functions with on-board safety terminals without intricate additional circuits. As a modular single-axis drive with servo functionality, SINAMICS S110 covers a power range from 0.15 HP (1-ph AC 230V) to 125 HP (3-ph AC 480V).
The SINAMICS S110 can be used to position both synchronous servomotors and induction motors.
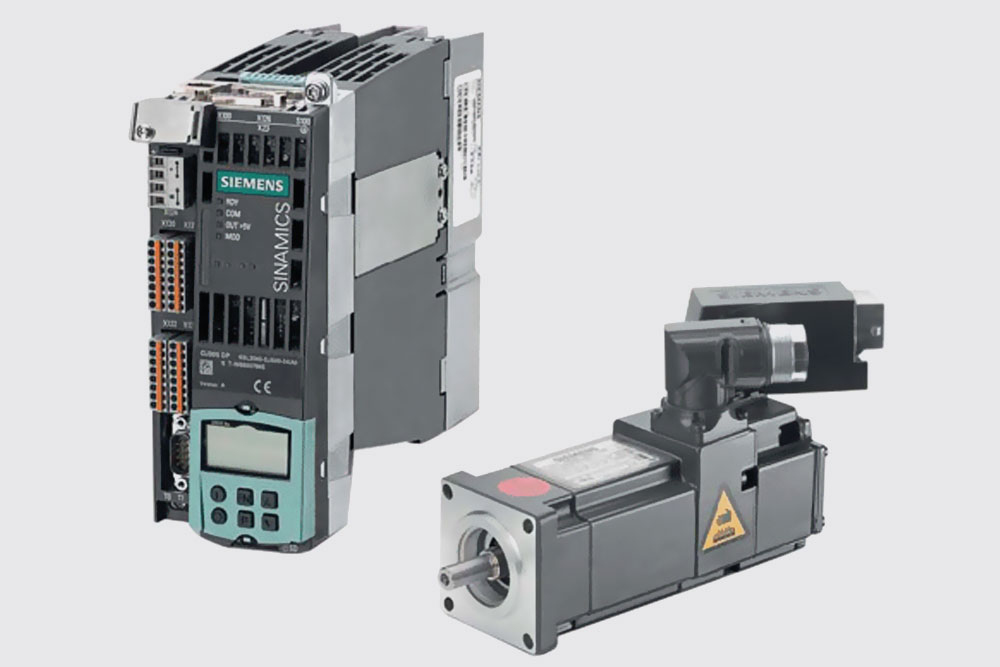
SINAMICS S110 Typical Applications :-
Handling equipment
S120 Drive
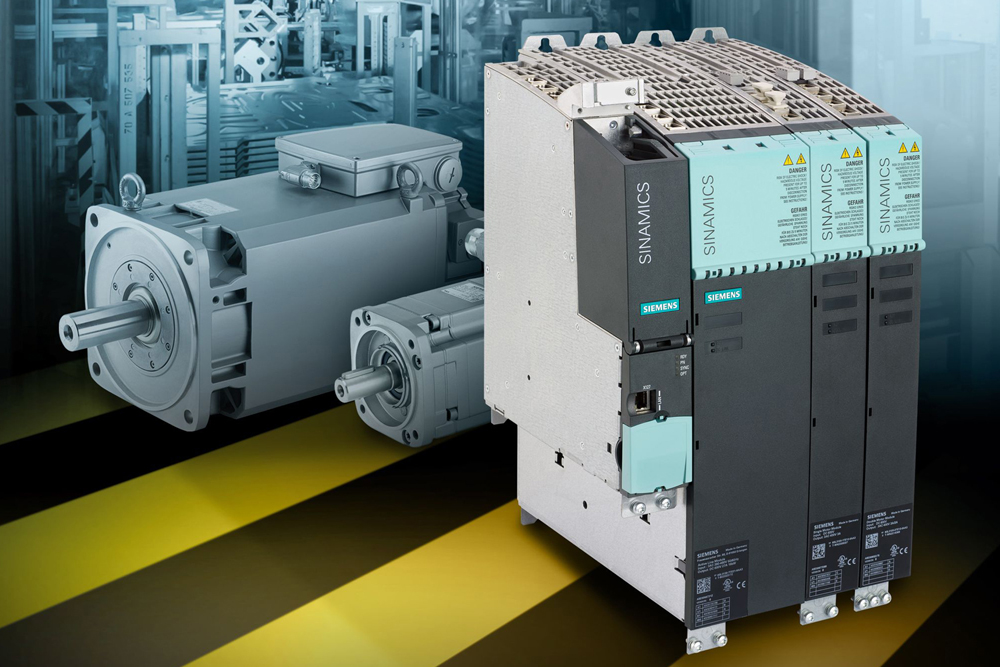
For single-axis drives, the line infeed and the power supply of the motor are combined in one device – the Power Module. For single-axis applications, the closed-loop drive control is handled by a special Control Unit (e.g. CU310-2) mounted on the Power Module; for multi-axis applications, using a Control Unit (e.g. CU 320-2) coupled via DRIVE-CLiQ. In the latter case, instead of the Control Unit, a CU adapter is mounted on the Power Module.
AC-Drives are each equipped with a CU310-2 Control Unit for coupling to a higher-level control. It offers functions from a basic speed controller up to extensive positioning functions. CU310-2 DP with PROFIBUS DP connection or CU310-2 PN with integrated PROFINET interface are available.
Drive-related inputs/outputs in the Control Unit can be simply logically combined using BICO technology. As a consequence, the highest possible degree of decoupling between the drive and higherlevel control system can be achieved. For AC-Drives, when required, an additional encoder and drive-related I/O can be connected via DRIVE-CLiQ
The drive is connected to a multi-axis Control Unit, e.g. CU320-2, using the CU adapter CUA31 via the DRIVE-CLiQ interface. This Control Unit then handles the drive functions for the AC-Drive. In this configuration, SINAMICS S120 AC-Drives can also be used in mixed operation with SINAMICS S120 multi-axis devices. This facilitates maximum flexibility when using SINAMICS S120 devices. In comparison to the CUA31, the CUA32 also has an integrated HTL/TTL encoder interface to connect an external encoder.