Refined Iodised Salt Processing Plant
INTRODUCTION
Main source of salt is rocks, sea & lake. Maximum consumption of salt is in its natural form after being produced from sea or directly from rock. But with time, awareness of uses of salt have grown manifold and the demand of refined iodised salt is increasing tremendously during the last few years. Refining not only helps in increasing purity of salt but also improves flow-ability and use of anti-caking agents helps in keeping quality too. During refining and drying process iodisation is done which is important for human body to avoid various diseases. Refined salt is further graded for various applications like kitchen salt, table salt and industrial salt.
SALT REFINERY ARE MAINLY OF TWO TYPES:
- Mechanical Refinery.
- Vacuum Refinery
MECHANICAL SALT REFINERY
Crude Salt is fed into the feeding hopper of suitable capacity and it is then transferred to a belt conveyor. This belt conveyor will be fitted with a magnet to remove rubbish metal and will also be provided with a belt weigher with totaliser. Crude salt is pre-washed in special washing system. This is then fed to the feed in hopper of the wet mill for grinding. Wet mill is used to grind the salt with the help of saturated brine solution. This mixture is then passed to the slurry tank that is fitted with a slow speed agitator.
This slurry is then pumped through centrifuges, high pressure pump, centrifugal pumps, axial flow pumps, gear pump to the wash tank by a slurry pump, wherein dirt is removed from the slurry. The overflow from the wash tank is collected in a clarifier wherein brine is clarified and re-circulated in the plant. This is then pumped to the hydro cyclone by a slurry pump for thickening of the slurry.
MECHANICAL SALT REFINERY SYSTEM
( FLOW DIAGRAM )
![]() ![]() |
![]() ![]() |
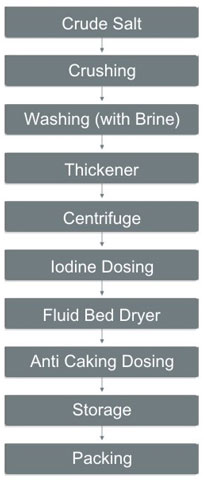
DRYING & FINISHED PRODUCT HANDLING SECTION
The salt crystals from the centrifuge are dried in a Fluid-Bed Dryer. The crystals forms a layer on the perforated sheet present in the drying chamber of the fluid bed dryer and is dried by means of hot air from a thermic fluid air heating/Indirect air heating system. The fines are removed from the exhaust stream in the cyclone separator and is collected separately. Dry salt is from the outlet of the fluid-bed dryer and is passed to the sifter through a bucket elevator. The oversized salt is separated in the sifter and the over sized salt crystals is passed to the pin mill for further grinding and salt is passed to the feed in hopper of the blender wherein free flowing agent is added. This free flowing salt is then sent to the storage silo for packing.
VACUUM REFINERY
The process involves dissolving of salt in water and making a saturated solution of salt. The saturated brine is pumped out to a brine clarifier, where the insolubles settles at the bottom of the clarifier and clear brine solution is taken to a brine tank. In the brine tank required chemicals are added to precipitate out magnesium and calcium salts present along with the salt. The brine is then filtered and taken to the final brine tank. From this tank saturated brine is fed to the continuous evaporation plant where Crystallisation takes place and slurry is pumped out to a concentrate tank. This salt slurry is then pumped to a hydro-cyclone battery to get a slurry concentration up to 50-60%. This slurry is fed to a centrifuge, and from the centrifuge salt cakes with 4-5% moisture comes out. The salt with 4-5% moisture is fed to a fluid bed dryer through a screw conveyor where the iodisation is completed.
In the Vibro Fluid Bed Dryer, the salt is fluidized by hot and atmospheric air for drying and cooling the salt. The salt is then taken through a bucket elevator to a sieving machine. The oversize particles are collected and sent for re-dissolving in the final brine tank. To the crystallined salt is then added the free flowing agent in a screw mixer and finally sent to a storage silo.
The salt packaging is done from the silo by a FFS machine in 1 kg. Packs or it can be packed in bags as per requirement.
VACUUM SALT REFINERY SYSTEM
( FLOW DIAGRAM )
![]() |
![]() |
![]() |