Effluent Treatment Plant for Textile Dyeing Industry
ETP SYSTEM FOR TEXTILE DYEING INDUSTRIES
Textile dyeing industries need huge quantity of water for textile dyeing, which they normally pump out repeatedly from the ground or natural water sources resulting in depletion of ground water level.
In the dyeing process textile industries generate huge quantity of toxic effluent containing colours, sodium sulphate, sodium chloride, sodium hydroxide and traces of other salts. These are generated after dyeing and after washing of garments / fabrics. After dyeing the waste water produced is called Dye Bath water and after washing the waste water generated is called wash water. Dye Bath contains higher solids in the range 4-5% whereas wash water contains only 0.5-1% solids.
Based on the above mentioned fact “SSP” has developed a technology which can process such harmful toxic effluent water and transform it into reusable water. Thus the textile industries will have the advantage of using the same water in the dying process repeatedly, also the salt used for dyeing can be reused or sold in the market.
The technology offered by SSP can overcome all problems pertaining to environmental pollution in respect to textile dying industries.
The basic thrust of the technology is to convert entire quantity of effluent to zero level by separating water and salt using evaporation and separation technology.
The concept and the treatment is based on the removal of the entire COD/BOD and the condensate coming out to meet the fresh water quality requirement in the process.
TEXTILE WASTE WATER HANDLING BY EVAPORATION AND SOLID SEPARATION BASIC PRINCIPLE:
The technology is based on basic principle of reduction of quantity by concentrating the effluent and subsequently separation of salt and water.
THE EVAPORATION PROCESS:
Textile Effluent is fed to the vacuum evaporator to concentrate up to 40% solids concentration. The total process is under vacuum and the vapors generated in the system are re-used to economize steam consumption in multiple effect evaporation system with thermal vapour recompression system. The thermal vapour recompression system use Vapours generated in the evaporator and compress it by steam and the compressed vapours are used as heating medium in the evaporator, in this way steam consumption is reduced. Water recovered from the evaporator has low COD/BOD value and can be recycled in the plant.
SEPARATION PROCESS
(ZERO LIQUID DISCHARGE SECTION):
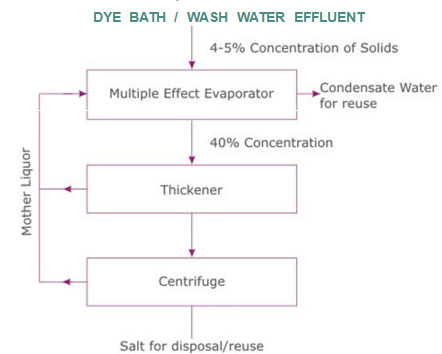
The resultant slurry (concentrate) is fed to the thickener and centrifuging section for converting the liquid concentrate to solid waste. The mother liquor from thickener and centrifuge is recycled back to evaporator.
The water separated out from evaporator is good enough in quality to recycle in the plant for Dyeing.
KEY FEATURES:
- Zero Liquid Discharge
- Fully Customized Designed System
- Highest Steam Economy
- Low Operating Cost
- Less Downtime for Maintenance
- Generation of Reusable Condensate Water
- Operator Friendly