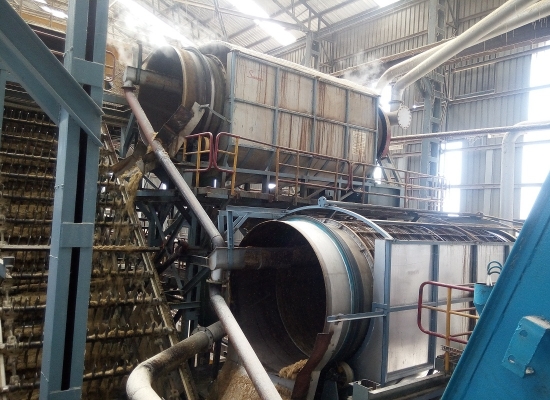
2 Stage Rotary Juice Screening system
At the outset, thanks to mill engineer colleagues, sincerely appreciating their consistent and best efforts to maximize the P.I. of prepared sugarcane indeed for the good reason and with the good intention of further improving mill extraction performance and surely which is “A need of the Time”.
However it is being observed that well prepared sugarcane with the long thread like formation of sugarcane fiber at sugarcane preparatory device for rupturing of sugarcane cells is already a story of the past and that, more and more powdered dust like formation of sugarcane fiber is unintentionally and unavoidably found to be occurring in almost all sugar factories. It is later observed that higher quantity of this finely pounded fiber is found to be escaping through 0.45/0.5 mm wedge bar opening which indeed is a universally accepted or opted norm of wedge bar gap by cane-sugar industry all over world.
This resulted into creating serious processing problems at clarification house as well as causing mechanical problems like choking at pumps, Juice heater headers and at wide gap PHE.
The problem was found further aggravated when these fine light weight fiber particles started appearing in sugar-cane clear juice the phenomena which was very rarely used to be observed in earlier times so much so that the final product white sugar was also found containing these fiber particles thus seriously deteriorating the quality of plantation white sugar due to sugarcane fiber contamination.
It was then felt necessary by cane-sugar industry that to provide ‘prior’ fool proof preventive measures for the effective separation of these fine sugarcane fibers at milling station or sugar cane diffuser where sugar from sugar-cane is extracted and never to allow them to enter into sugarcane juice clarification house at all. At the same time the system should be “cost effective” allowing immediate and forever recurring returns.