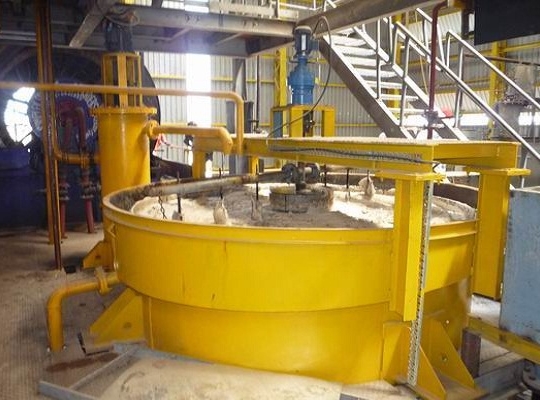
Syrup and Melt Clarification System
Introduction
The syrup resulting from evaporator station contains various organic matter in colloidal form and colouring matter derived from clear juice added with colouring matter further developed during evaporation and as such needs special attention for removal of various impurities so that the final product i.e. plantation white sugar will have minimum colouring matter adsorbed in the inter crystalline layers. While syrup sulphitation gives a bleaching effect and many more multifold advantages it has now become generally adopted practice to resort to a syrup clarification system which can consistently produce sugar of colour value much less than 100 IU. Syrup Clarification System is also used for producing raw sugar of much better quality.
Operation
Calcium Tri-phosphate is universally known as best colour adsorbent and obviously the first step in the system is production of calcium tri-phosphate by treating the syrup with lime sucrate and phosphoric acid in a specially designed reaction vessel to accomplish the reaction with provision of optimum reaction time for completion of the reaction.
The next step is aeration of the syrup by inducing micronized air which by virtue of its fine size adhere to calcium phosphate precipitate and other insoluble impurities. In the specially designed floatation clarifier the air bubbles are allowed to have a shortest path to the surface and the clarified syrup is withdrawn at the silent zone. The air bubbles after reaching to the surface burst into air and the scum which is accumulated on the top of the surface is continuously pushed by raker arms into scum channel. In order to activate the floatation phenomenon a floatation polymer which enhances kinetics of floatation is added prior to clarifier. Although major part of colouring matter gets adsorbed in the calcium tri-phosphate the part which still remains in the soluble form is precipitated by effectively mixing with de-colorising agent. The beauty of our system is that it is independent of any proprietary chemicals and as such there is no dependence on a particular brand. This further allows economic level of chemical consumption. This clarification method is adopted for sugar melt clarification as well, by incorporating appropriate design features.
Process automation at Syrup and Melt Clarification
The system is provided with complete PLC based process automation compatible to DCS/SCADA in respect of uniform flow, pH control and controlled addition of all chemicals w.r.t. flow rate. The electric motor drive of chemical dosing pumps are provided with VFD. The chemical is added in proportion to flow rate. The signal of flow meter is fed to ratio controller as input and the output of ratio controller is fed to VFD to vary the speed of pump for automatic dosing of chemicals at a pre-set value.
At floatation clarifier by virtue of difference between density of syrup or melt and that of scum containing insoluble solid impurities which are closely attached to fine micronized air bubbles the solid / liquid separation is effectively achieved.
However if further fine separation is desired for removing even the negligible quantity of very fine micron size particles then syrup or melt is subjected to fine filtration in a closed semi pressurised vessel provided with multi layers of assorted size gravel media layer initially of relatively higher size of say 20 mm and finally through 1.5 mm anthracite layer. The total cycle operation of inflow, run, back wash etc. are fully automated using PLC/DCS/SCADA based controls.
These filters prove very useful for producing refined sugar and also for production of value added plantation white sugar.