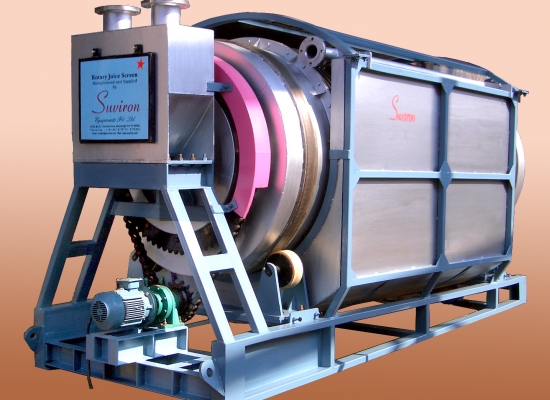
Rotary Juice Screen
Technology
Solid / liquid separation is effected on a welded wedge bar screen drum mounted in horizontal position with appropriate slope towards non-drive end. The diameter, the length of the screen, the speed of the rotating screen and its inclination are well designed to facilitate complete drainage of juice. Maximum juice is separated in feed section of the screen. Special design feature also includes cleaning the screen periodically by automatic application of hot water through flat cone nozzles which ensures clean screen surface throughout the operation period.
Construction
A cylindrical rotary drum fabricated in S.S. construction is fitted with rim / tyre located on either end for mounting the entire drum assembly on trunnions. The screening area comprises of welded wedge bar screen drums joined together by bolting arrangement.
Towards the drive end side of the end drum the driving sprocket is rigidly fixed on output shaft of gearbox and connected to driven sprocket mounted on rotating drum to transmit the power through heavy-duty chain arrangement. Thrust rollers fitted at the non-drive end absorbs the lateral thrust developed by inclined rotating drum. The entire assembly of the drum along with its trunnions is mounted on fabricated frame. Flat cone stainless steel spray nozzles are fitted on stainless steel piped header located on the framework of side hood to cover the entire length of screen drum. The drum along with screen is shop assembled and empty trial run of continuous 48 hrs. is conducted at workshop prior to dispatch.
Operation
The unscreened juice containing suspended solid particles comprising fine and coarse bagasse particles enters continuously from drive end of the drum through a distributor. The screened juice is collected in the sloping half cylindrical shape bottom trough for quick removal of screened juice to screened juice receiving tank. The solid mass keeps on rolling on the wedge bar screen and during its forward movement towards non-drive end the remaining juice is also drained away leaving the solid mass on the screen which is discharged to cane / bagasse blanket by gravity.
Capacity and sizing
Our production range offers design and manufacture of ONE single unit to suit upto 12000 TPD cane crushing capacity. For diffuser unit of extraction, a “totally closed” and fully insulated version of RJS is used to avoid the thermal loss that may occur due to hot draft juice and press water. This featured rotary screen is also used for Hot Melt Liquor Screening in refinery.