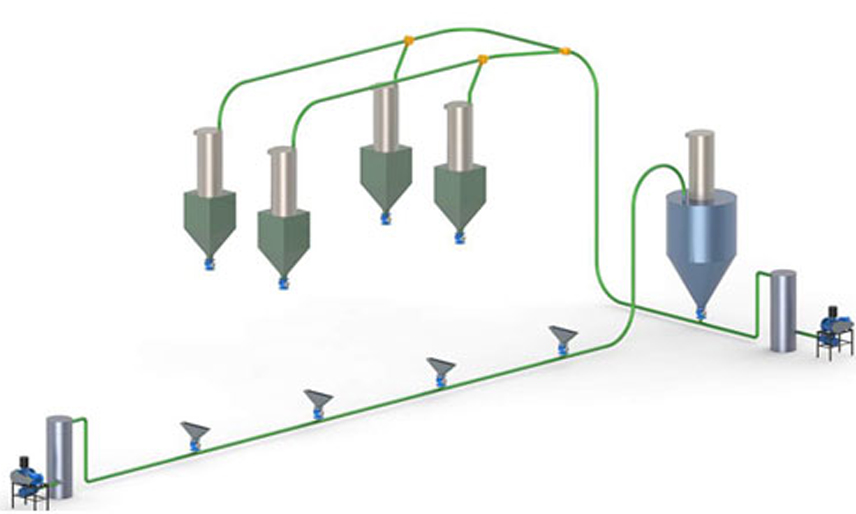
Pneumatic Conveying System
A Pneumatic Conveying System is a process by which dry powders or granules are transported or carried utilizing a gas from a source to a destination. The bulk materials are transferred through an enclosed conveying pipeline by the collective force of pressure or vacuum and the gas used (commonly air).
Depending on the product characteristics, gas volume & pressures are applied at design stage. This parameter categorises the systems as either LEAN Phase Pneumatic Conveying System or DENSE Phase Pneumatic Conveying System.
- Lean Phase
- Dense Phase
- Advantages
- Industries Served
Lean Phase
Lean Phase Conveying occurs when a material is conveyed in suspension in the following air. Lean phase is characterized by high velocity, low pressure (<1 bar) & Low solid to gas ratio. Lean Phase Conveying occurs when a material is conveyed in suspension using Gas
Types of Lean Phase Conveying Systems are:
a. Lean Phase Vacuum Conveying
- Capacity: Up to 10 TPH
- Conveying Distance: 300 mtrs
- Density of material: 150-2000 Kg/m3
- Vacuum: Up to(-) 0.5 Bar
- Material handled: Chips , Fine Powder, Ash, Other low-density material, etc.
a. Lean Phase Pressure Conveying
- Capacity:Up to 35 TPH
- Conveying Distance: up to 200 meters
- Density of material: 150-2500 Kg/m3
- Vacuum: Up to 1 Bar
- Material handled: Powders, Sugar, Abrasive Material, Bulker Unloading, etc
Dense Phase
Dense Phase conveying occurs when material is conveyed in suspension by gas using lower velocities & High Pressure than those required for lean phase over all or part of the pipeline. It is often referred to as non-suspension flow. It is characterized by low velocity, High Pressure (>1 bar) and High Solid to Gas ratio.
- Capacity: Up to 300 TPH
- Conveying Distance: Up to 450 meters
- Density of material: 150-3500 Kg/m3
- Pressure: Up to 5 Bar
- Material handled: Highly Abrasive materials, Fly Ash, etc.
Advantages
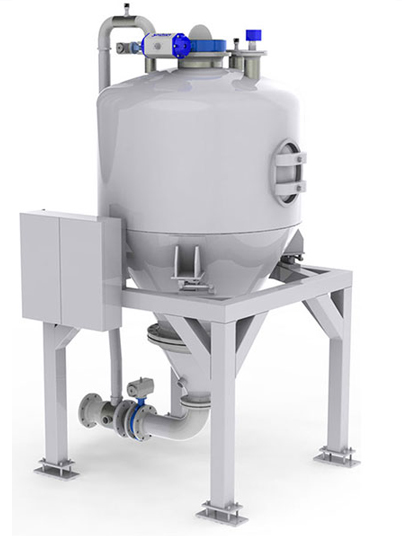
- High Reliability
- Precise conveying
- Dust Free operation
- Optimize Power consumption
- Hygienic operation
- User Friendly
- Completely Automatic System
- Less man power required
- Optimize space requirement
- Handle many different solids (Abrasive, Corrosive, Combustible, etc)
- Closed Loop Inert Gas Conveying available
- Multiple feed and discharge point can be given
Industries Served
- Food & Pharmaceuticals
- Steel
- Chemical & Petrochemical
- Cement
- Power Plant
- Refinery
- Agro Based /Sugar/ Rice/ Tobacco
- Breweries and Distilleries
- Paper and pulp
- Textiles
- Soaps, Detergents & Waxes
- Non-Ferrous Metallurgy
- Paints, pigments and Dyes etc.