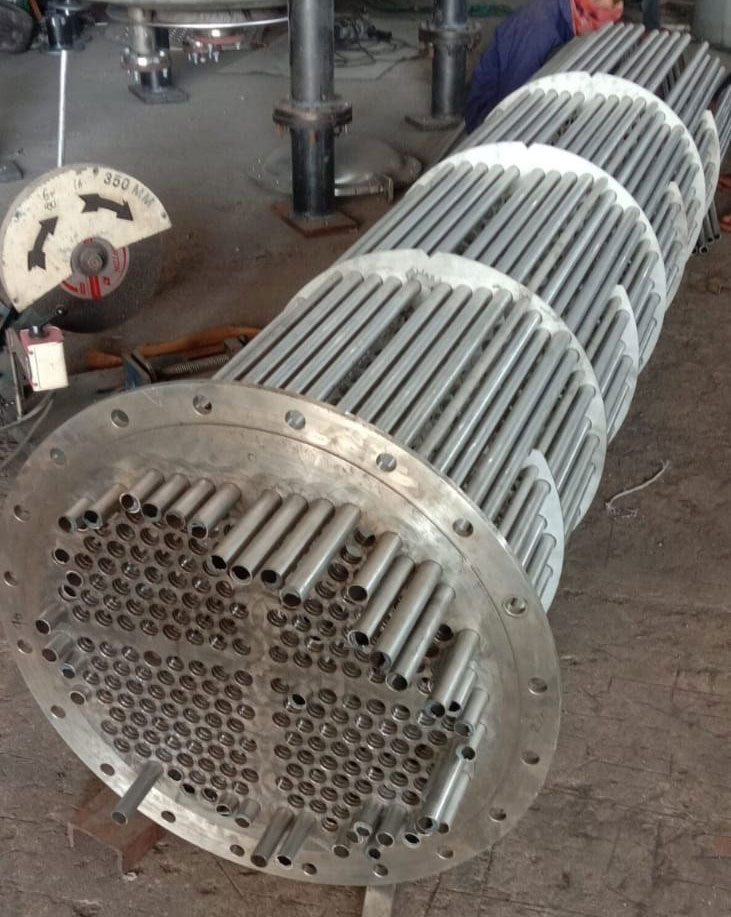
Heat Exchangers
TECHPERT Process Industrieshas technical expertise in process and mechanical design of Heat Exchangers. We have design expertise in Heat Exchanger for specific customer applications to achieve desired output parameters. Our design and manufacturing is compliant with TEMA Standards. Our Heat Exchangers are ranging from 5 M3 to 5000 M3 heat transfer area with variable operating ranges. We design heat exchangers in various metal alloys.We have straight tube, U tube and other designs also. Two fluids, of different starting temperatures, flow through the heat exchanger. One flows through the tubes (the tube side) and the other flows outside the tubes but inside the shell (the shell side). Heat is transferred from one fluid to the other through the tube walls, either from tube side to shell side or vice versa. The fluids can be either liquids or gases on either the shell or the tube side. In order to transfer heat efficiently, a large heat transfer area should be used, leading to the use of many tubes. In this way, waste heat can be put to use. This is an efficient way to conserve energy. Heat exchangers with only one phase (liquid or gas) on each side can be called one-phase or single-phase heat exchangers. Two-phase heat exchangers can be used to heat a liquid to boil it into a gas (vapour), sometimes called boilers, or to cool the vapours and condense it into a liquid (called condensers), with the phase change usually occurring on the shell side.. In large power plants with steam-driven turbines, shell-and-tube surface condensers are used to condense the exhaust steam exiting the turbine into condensate water which is recycled back to be turned into steam in the steam generator. They are also used in liquid-cooled chillers for transferring heat between the refrigerant and the water in both the evaporator and condenser, and in air-cooled chillers for only the evaporator. They various applications in Food, Chemical, Power and Pharmaceutical Industry.
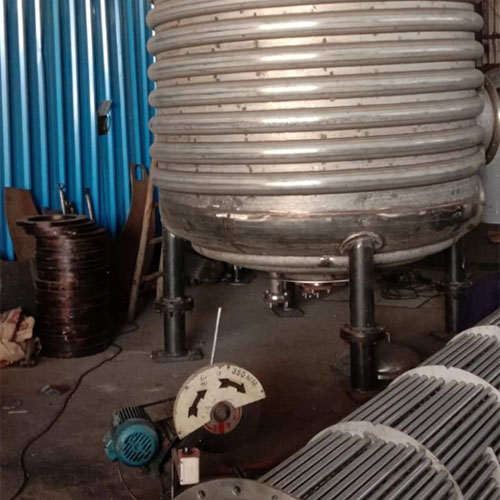
Reactors
TECHPERT Process Industrieshas technical expertise in process and mechanical design of Reactors. We have design expertise in Reactors for specific customer applications to achieve desired output parameters. Our reactors are ranging from 500 Kg/Batch to 20000 Kg/Batch capacity.Our reactors can be jacketed or with Limpet and with agitator. A chemical reactor is an enclosed volume in which a chemical reaction takes place.In chemical engineering, it is generally understood to be a process vessel used to carry out a chemical reaction,which is one of the classic unit operations in chemical process analysis. The design of a chemical reactor deals with multiple aspects of chemical engineering. Chemical engineers design reactors to maximize net present value for the given reaction. Designers ensure that the reaction proceeds with the highest efficiency towards the desired output product, producing the highest yield of product while requiring the least amount of money to purchase and operate. Normal operating expenses include energy input, energy removal, raw material costs, labor, etc. Energy changes can come in the form of heating or cooling, pumping to increase pressure, frictional pressure loss or agitation.
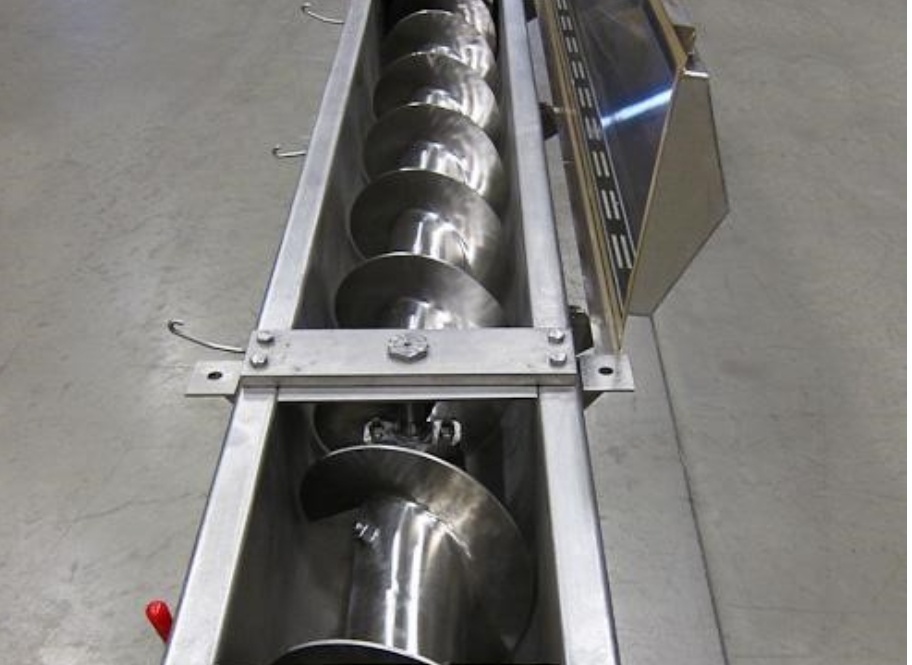
Screw Conveyors
TECHPERT Process Industrieshas technical expertise in process and mechanical design of Screw Conveyor. We have design expertise in Screw Conveyor for specific customer applications to achieve desired output parameters. Our Screw Conveyor are ranging from 500 Kg/Hour to 50000 Kg/Hour capacity. Shafted screw conveyors are used for various industrial applications. Main function of screw conveyor is to transfer material from one process to another. They are easy to operate, low maintenance and cost effective. They are ideal for handling dry free flowing to semi fluid materials. They can come in tubular or semicircular with trough design.
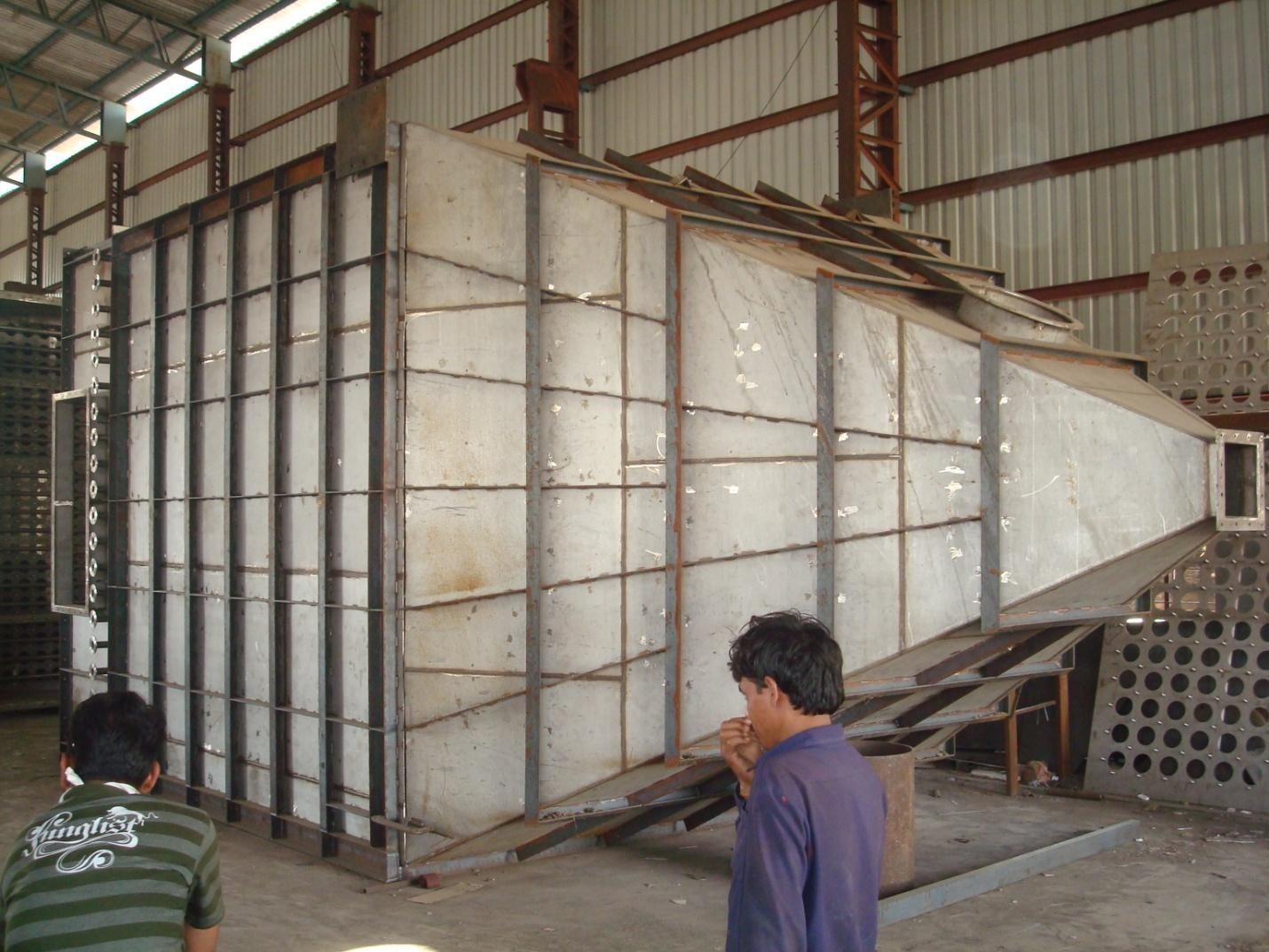
Pulse Jet Bag Filter / Dust Collector
TECHPERT Process Industrieshas technical expertise in process and mechanical design of Pulse Jet Bag Filters. We have design expertise in Pulse Jet Bag Filters for specific customer applications to achieve pollution control norms. Our Pulse Jet Bag Filters are ranging from 500 M3/Hour to 500000 M3/Hour capacity. The pulse jet bag filter consists of the filter bags housed in a casing or cage. The filter bag's material can vary depending on application. Pleated bags can be used to reduce overall equipment size. The filter bag house has a conical hopper at bottom with a discharge valve, to continuously remove the dust that is collected on the bags. The entire unit is mounted on structure. The dust laden air enters through the hopper with the help of suction fan. The heavier dust particles fall off at the entry, while the lighter dust goes upwards to the bags. The dust gets deposited on the outer surface of the bags and the clean air moves upward from the center of the bags to the plenum and to the top air outlet. The dust collected on the outer surface of the bags is removed in a pre-determined cycle by a momentary pulse of high-pressure compressed air through actuated valves. This is achieved by sequential timer wherein we can set pulsing time. The dust deposition formed on the bag surface slides down in the form of flakes. The cages help the bags retain their original shape once the effect of the compressed air is gone. The dust slides down the hopper walls to the rotary air lock valve.
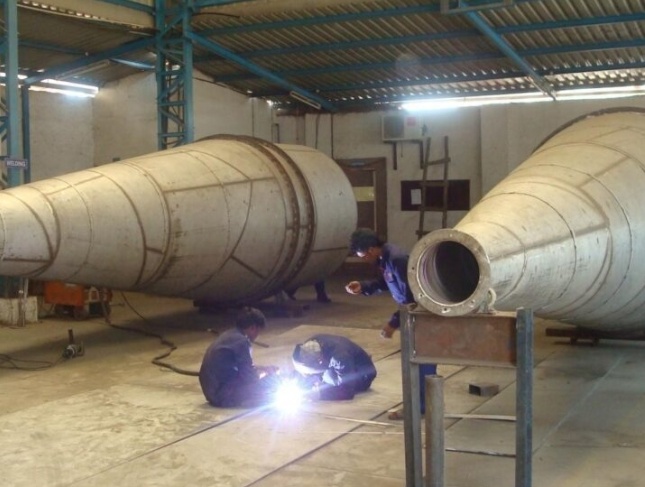
Cyclone Separator
TECHPERT Process Industrieshas technical expertise in process and mechanical design of Cyclone Separator. We have design expertise in Cyclone Separator for specific customer applications to achieve pollution control norms. Our Cyclone Separator are ranging from 500 M3/Hour to 500000 M3/Hour capacity.Higher capacity cyclones are designed in Duo/Triple or Quadruple construction. Essentially the function of a cyclone separator is to remove the majority of the dust and debris from the air stream that carries it. It does this by introducing the dust filled air to the cyclone chamber via an inlet mounted tangentially to the cylinder at the top. This causes the air and dust to circulate around the periphery of the container, and as such centrifugal forces keeps the particulate matter to the outside edges. The cyclone profile forces the air stream and dust particles down into the conical shaped container where the cone shape creates a cyclone with higher centrifugal air speed. This higher air speeds in the cone will throw the dust particles, both large and small, off to the side and the clean air is vented out.