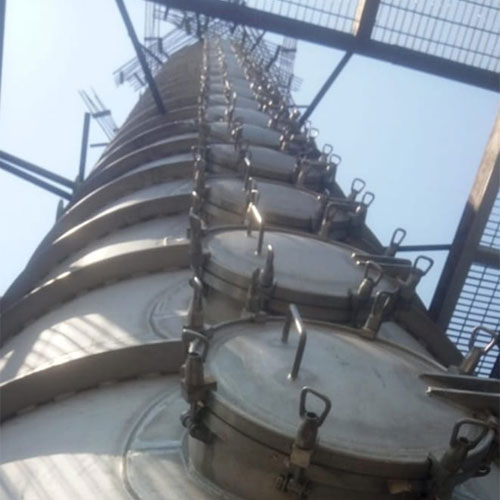
Fractional
TECHPERT Process Industrieshas technical expertise in process and mechanical design of various Fractional Distillation Columns. Fractional distillation is the separation of a mixture into its component parts, or fractions. Chemical compounds are separated by heating them to a temperature at which one or more fractions of the mixture will vaporize. It uses distillation to fractionate. Generally, the component parts have boiling points that differ by less than 25 °C (45 °F) from each other. We have design expertise in manufacturing chemical, petrochemical and pharmaceutical distillation columns of various capacities. Industrial distillation is typically performed in large, vertical cylindrical columns known as "distillation or fractionation towers" or "distillation columns" with diameters ranging from about 0.65 to 6 meters and heights ranging from about 6 to 60 meters or more. The distillation towers have liquid outlets at intervals up the column which allow for the withdrawal of different fractions or products having different boiling points or boiling ranges. By increasing the temperature of the product inside the columns, the different products are separated. The "lightest" products (those with the lowest boiling point) exit from the top of the columns and the "heaviest" products (those with the highest boiling point) exit from the bottom of the column. Large-scale industrial towers use reflux to achieve a more complete separation of products. Reflux refers to the portion of the condensed overhead liquid product from a distillation or fractionation tower that is returned to the upper part of the tower.
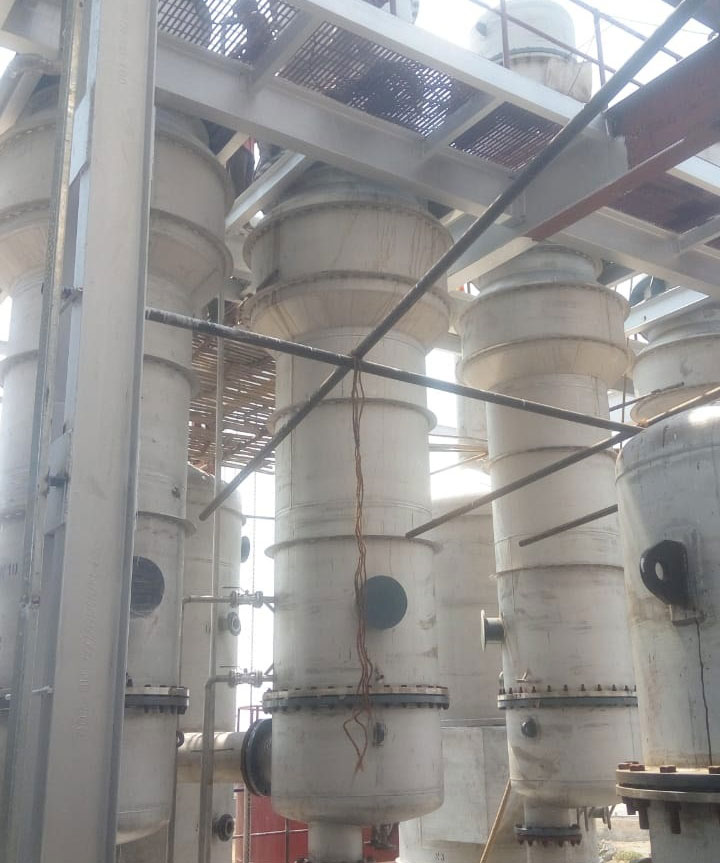
Vacuum
TECHPERT Process Industries has technical expertise in process and mechanical design of various Vacuum Distillation Columns.
Vacuum distillation is distillation performed under reduced pressure, which allows the purification of compounds not readily distilled at ambient pressures or simply to save time or energy. This technique separates compounds based on differences in their boiling points. This technique is used when the boiling point of the desired compound is difficult to achieve or will cause the compound to decompose. Reduced pressures decrease the boiling point of compounds. The reduction in boiling point can be calculated using a temperature-pressure graph Industrial-scale vacuum distillation has several advantages. Close boiling mixturesmay require many equilibrium stages to separate the key components. One tool to reduce the number of stages needed is to utilize vacuum distillation. Vacuum
distillation can improve a separation by:
• Prevention of product degradation or polymer formation because of reduced pressure leading to lower tower bottoms temperatures, Reduction of product degradation or polymer formation because of reduced mean residence time especially in columns using packing rather than trays.
• Increasing capacity, yield, and purity.
Another advantage of vacuum distillation is the reduced capital cost, at the expense of slightly more operating cost. Utilizing vacuum distillation can reduce the height and diameter, and thus the capital cost of a distillation column.
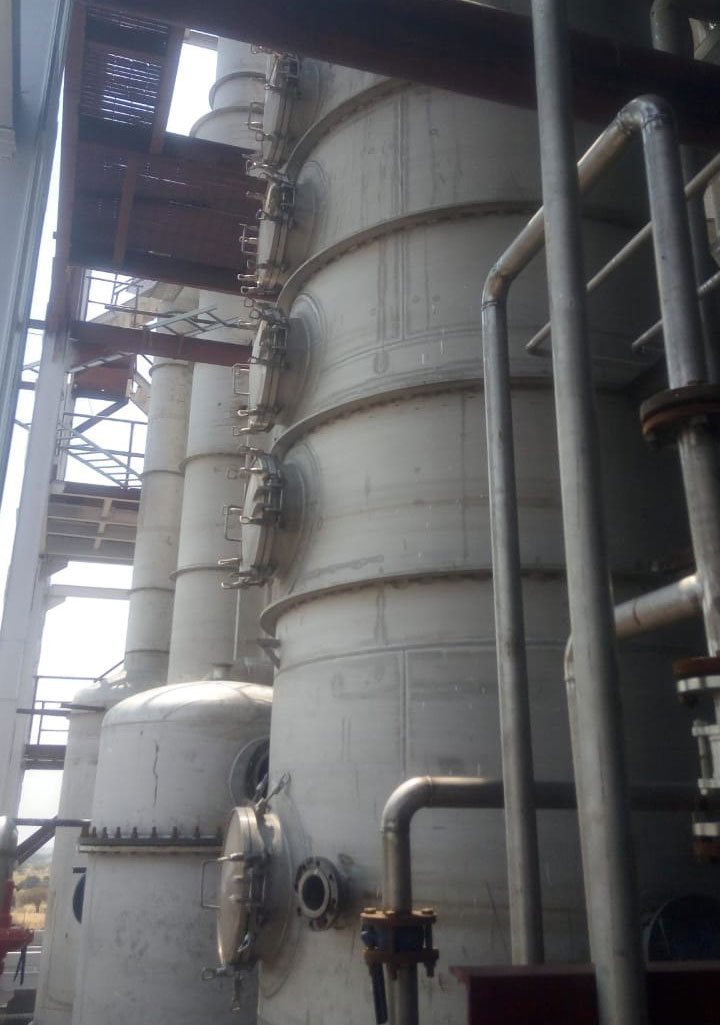
Molecular sieve
TECHPERT Process Industries has technical expertise in process and mechanical design of various Molecular Sieve Distillation Columns. A molecular sieve is a material with pores / holes of uniform size. These pore diameters are similar in size to small molecules, and thus large molecules cannot enter or be adsorbed, while smaller molecules can. As a mixture of molecules migrate through the stationary bed of porous, semi-solid substance referred to as a sieve (or matrix), the components of highest molecular weight (which are unable to pass into the molecular pores) leave the bed first, followed by successively smaller molecules. The diameter of a molecular sieve is measured in nanometres (nm). It is used to achieve high purity and removal of water. Methods for regeneration of molecular sieves include pressure change, heating and purging, or heating under high vacuum. Regeneration temperatures range varies depending on molecular sieve type.
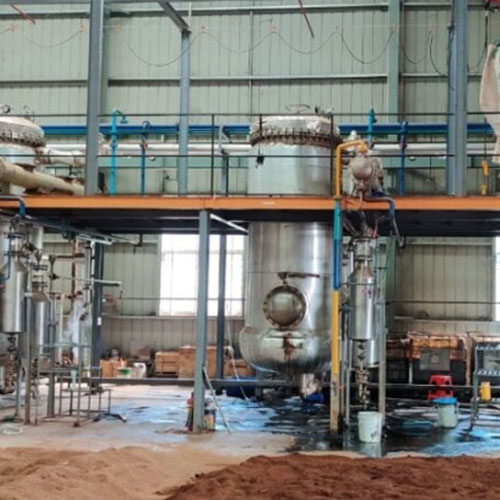
Essential Oil Steam Distillation
TECHPERT Process Industries has technical expertise in process and mechanical design of various Steam Distillation systems which are batch type. Our capacities range from 200 kg to 1000 kg loading in single batch. If more capacity is required, then one has to add more charging vessels. Steam distillation is carried out by passing dry steam through the plant material whereby the steam volatile compounds are volatilized, condensed and collected in receivers. Steam distillation has been in use for essential oil extraction for Geranium, Turmeric, Curcumin, Ginger and many others. Hydro-steam distillation is carried out when the perfumery plant material is susceptible to direct steam. In this technique the plant material is supported on a screen or a perforated grid placed at some distance above the bottom of the still. Distillation is carried out with low pressure steam which replaces the volatile compounds from the intact plant material.