Aarti Hydrogenator
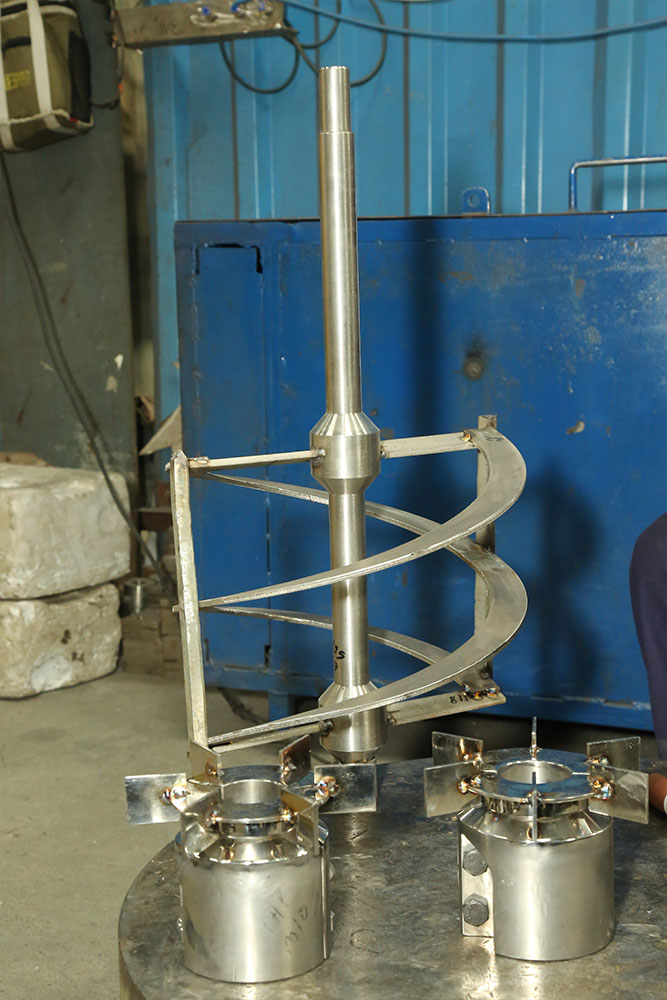
In gas-liquid reactions like hydrogenation which takes place in presence of solid catalyst, the resulting mass transfer is more important than the reaction itself. Especially, when we scale up the reaction to a larger commercial capacity, we can face many issues such as increased reaction time, formation of by-products due to the insufficient mixing in the reactor, lesser mass transfer due to low gas holdup.
For this kind of multiphase reaction, the selection of the agitator is critical in the design of an industrial reactor. Generally, there are two types of impellers in a Gas-Liquid-Solid mixing applications, i.e. (a) Gas dispersion impeller and (b) Axial pumping impeller to increase the gas holdup inside the reaction mass. In the standard impeller arrangement, the gas is introduced below a high shear impeller such as six bladed curved blade turbine which breaks the gas bubbles to a smaller size and increases the surface area for efficient mass transfer.
The impeller accomplishes this by creating large velocity gradients or shear rates, to break the gas into smaller bubbles. It has been reported that the total batch time in the scaled up reactor decreased more than two times and the catalyst life increased five times by changing the arrangement and type of impeller. Thus, we need to select the impeller configuration properly to get the desired results.
The Root Cause
To identify the main issue behind this inefficiency, our R&D team worked closely with our engineers and site engineers, and the following information was identified
- For a dead-end type hydrogenation reaction, we need maximum consumption of Hydrogen gas. This can be accomplished by increasing the gas holdup in the reaction mass using an axial flow impeller near the surface of liquid which will reintroduce the unreacted gas leaving through the surface.
- In another arrangement, the gas was introduced through the holes at the bottom of a hollow pipe shaft, and into the flow regime of the bottom-most impeller. This type of arrangement is efficient only up to 5 KL reactor capacity as for higher capacity reactors, it results into zone formation.
- Further, it was reported that the impellers producing a vortex effectively induce the gas from the gas-liquid interface into the liquid. It is suggested that in using dual impellers in a dead-end hydrogenation process, it is more efficient to install an axial-flow impeller at the upper position and a radial-flow impeller at the lower position along with a half-baffle.
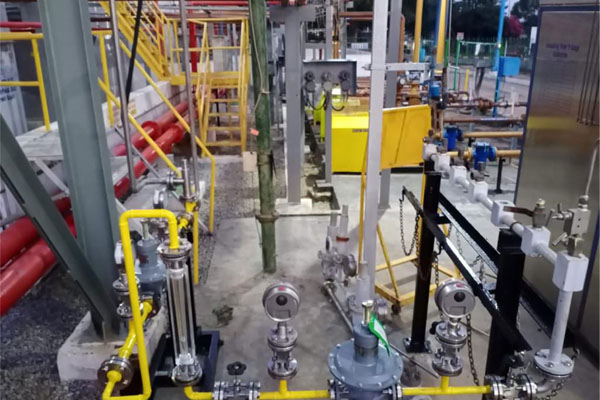
To overcome this issue, the gas can be introduced at the bottom of each impeller using gas induction pipes.
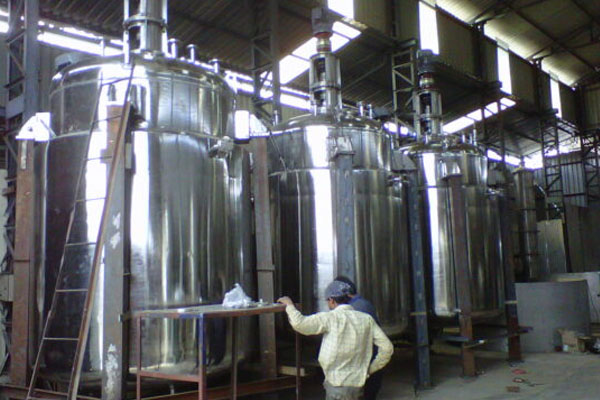
While Browsing Through The Available Literatures, Some Of The Designs Of Batch Reactors For Hydrogenation Were Reviewed As Follows..
- Decreasing the gas bubble size, thereby increasing the total interfacial area of the gas
- Increasing the gas-liquid interface turbulence, thus reducing the liquid film resistance
- Giving a uniform gas concentration throughout the tank contents
- Increasing the time each bubble spends in the liquid.
Case Studies
In 2011 ACME supplied a three stage impeller system agitator to Aarti Industries Limited for 1KL Hydrogenator with a combination of BT-601 impeller at the bottom, AA-405 Hydrofoil impeller at the middle and 4 bladed PBT at the top. In this new impeller system, CBT-601 promotes the required Radial flow and shear which decreases the gas bubble size and increases the gas-liquid interface turbulence.
AA-405 Hydrofoil impeller imparts axial flow which improves gas-liquid-solid contact by enhancing the suspension of the catalyst, improving overall blending and heat transfer. While a 4 bladed PBT forms a vortex at the top of liquid level resulting in remixing of escaping gas in to the reactant mass from the head space.
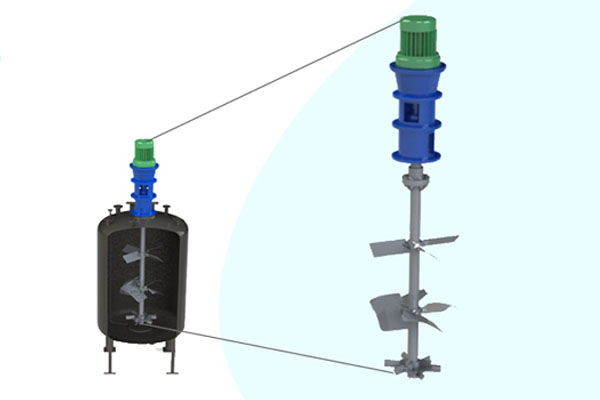
Hydrogenator Agitator System Supplied By ACME
Earlier the same hydrogenator was equipped with a gas-induction type impeller system agitator, where motor power was 3.7 KW and impeller speed was 325 rpm. The motor rating of agitator supplied by ACME was same i.e 3.7 KW but the impeller speed was reduced to 230 rpm. This agitator was installed on the Aarti Industries Limited for 1KL Hydrogenator and hydrogenation reaction batches were performed.
After the completion of reaction batches it was observed that, with old gas-induction impeller agitator the reaction batch completion time was 55-60 hours on an averaged was reduced to 24 hours on an average for the same process with same power consumption. These results concluded that the given agitator with combination of three stage impeller system reduce the batch time by 60% for the given application as compared to old gas-induction impeller agitator for no additional power input producing significant cost savings in Energy input and Catalyst utilisation.
The customer was well satisfied with the performance and benefits of the agitator with three stage impeller system technology supplied by ACME Process Systems Pvt Ltd and has replaced all the other gas-induction impeller agitator for same application at different plant sites.
Till date ACME has provided the same agitator of different capacity for various gas-liquid and solid-gas-liquid applications such as chemical reactions, hydrogenation, gas stripping, fermentation as well as waste treatment