Static Mixer
Static Mixers are one of the most energy-efficient, and maintenance-free mixers in the mixing industry. The necessary mixing capability happens due to the complex mesh or interlacing structures, that provide the materials such as chemicals, etc. to move through them at a pace right enough for maximum blending. Since there are no moving parts, and no additional electricity consumption by the mixers themselves, they are the chosen ones in various industries.
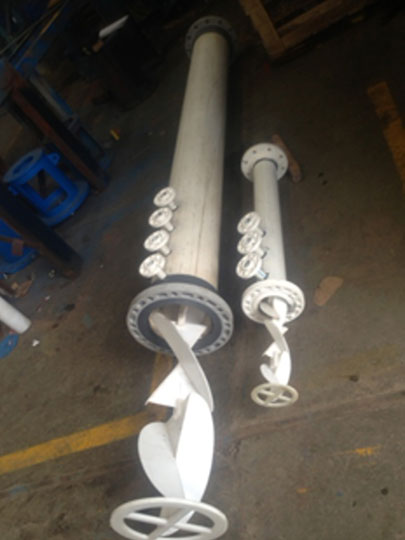
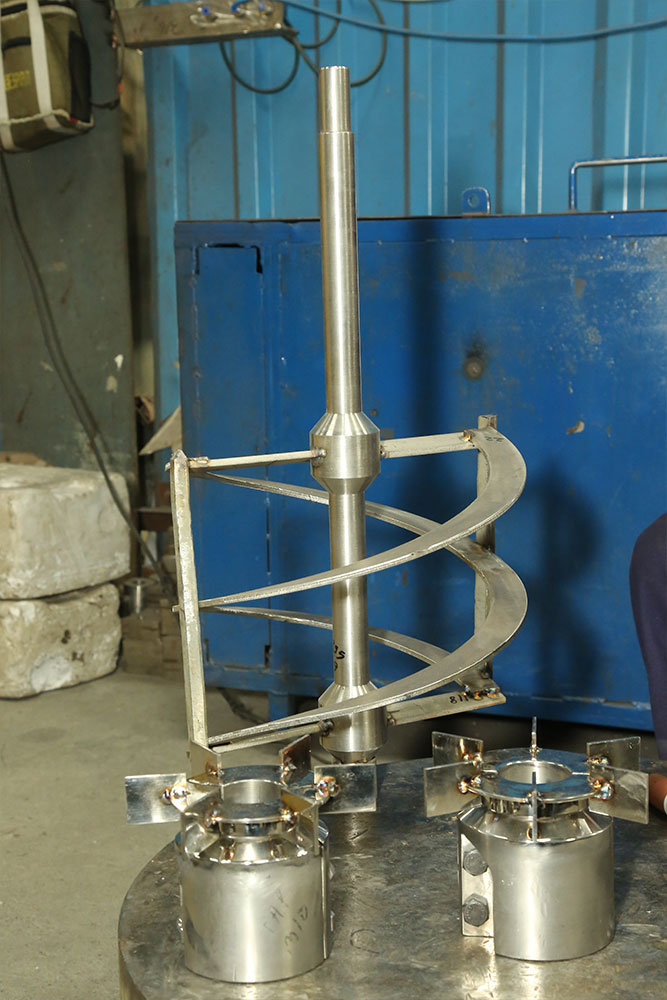
THE WORKING
Diagram: Streaming of liquids through a static mixer
A: Liquid 1
B: Liquid 2
C: Static Mixer with Red-coloured Mesh
As shown in the above figure, the red coloured mesh, normally referred to as the element/s, create multiple intermingling of niches and gaps. This sets mechanical dispersion of the stream, while the pressure of the stream itself causes diffusion. This repetitive and disruptive, yet continuous, flow ensures maximum and even blending between the liquids, which results in perfect homogenization. The homogeneity is governed by the nature of the liquids i.e. chemicals, additives, etc., their viscosity and other properties, type of the elements within the static mixer, the no. of such elements, and the length available for mixing. The degree of homogeneity is measured in terms of CoV – Coefficient of Variance
The industry CoV target for Static Mixers is around 0.05 i.e. 5% at length of 3 x pipe diameters from the mixer exit.
ACME has a wide experience in building static mixers that meet industry specific requirements for thorough blending of chemicals or additives with reaction mixture or water, dispersing liquid in the extraction process, neutralization of pH, etc.
ACME STATIC MIXERS eliminate unnecessary downtime, and enhance product quality and process control across pastes, slurries, liquid or gas.
ACME has been recognized across industries for providing customized products to its clients. Prior to designing the Static Mixers, ACME engineers study critical parameters of the process, such as viscosity, density, flow rate, pressure drop and the desired CoV, Reynold's number, flow type – laminar or turbulent. The static mixer is then designed and fabricated to meet the industry standards and the process requirements. Only high quality metallic MoC, such as SS304, SS316, SS316L, Hastelloy, other exotic materials, is used to ensure that the mixers perform in highly corrosive conditions, and for a longer time.
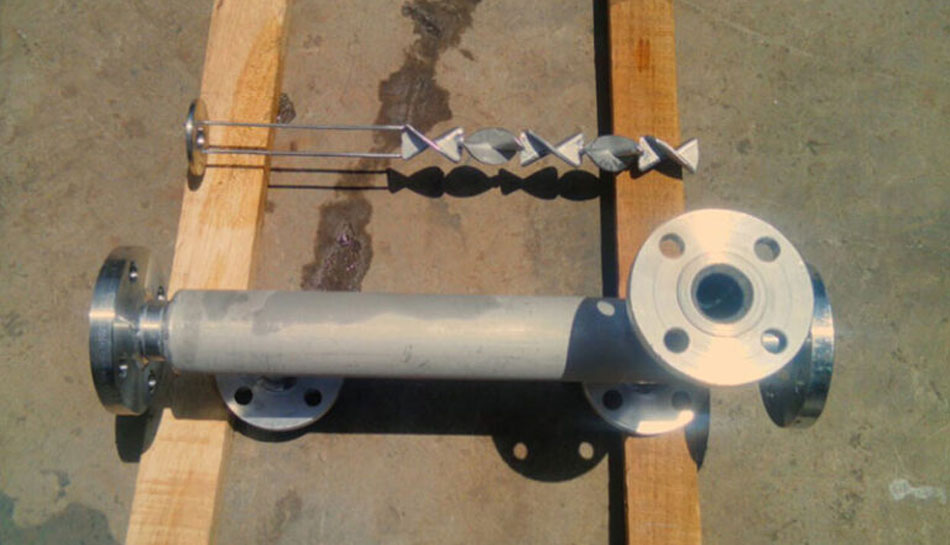