Roto Cone Vacuum Dryer (RCVD)
In industrial process systems, a variety of solid cakes or products are derived, after the filtration process, which need to be dried thoroughly. Further, some of these solids are amorphous and crystalline that have a tendency to degrade or oxidize at higher temperatures, which may be toxic in nature.
ACME Roto Cone Vacuum Dryer (RCVD) are a perfect solution to overcome these issues. These RCVDs are specially designed to dry products that are temperature sensitive, are susceptible to oxidation, volatile, and those that may be toxic in nature. ACME RCVDs are great substitutes to other types of dryers that cause air-contamination. ACME provides turnkey solutions covering design to fabrication, installation and commissioning of the entire RCVD plant.
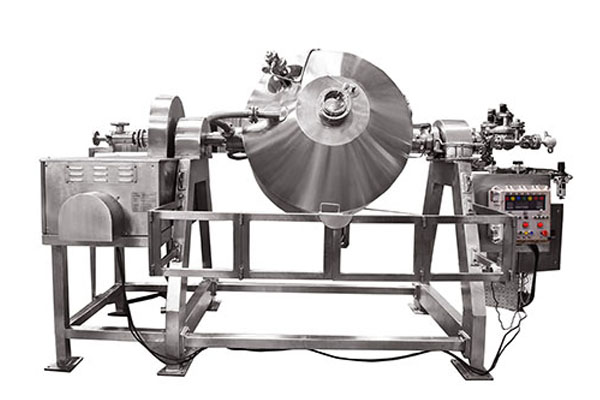
CONSTRUCTION & OPERATIONS
ACME RCVD consists of jacketed double conical chambers, mounted on robust pedestal, which rotates at very low RPM ranging from 5-10 RPM, as required by the process. For uniform drying of product, heat transfer fluids such as hot water or steam is circulated around the conical jacket. This completely jacketed system provides optimum dryer efficiency..
The special mechanical seals ensuring a perfect vacuum in the system are provided with the lump breaker shafts. Specially designed micro filters are installed in the dryer to prevent solids from escaping the system. The product is discharged through a butterfly valve mounted at the outlet nozzle, which can be automated or operated manually.
The material which is to be dried is charged as a batch. As the dryer rotates the wet material goes through a heating process by conduction and agitation, with gentle tumbling action, and while maintaining vacuum inside the drying chamber to achieve rapid drying. The vacuum inside the chamber decreases the vapour pressure of the solvent thereby reducing the product solvent boiling point. The solvent evaporates quicker and enhances the rate of drying. The solvent vapour is then pumped out through vacuum exhaust pipe.
A well designed sealing system ensures maintenance of required vacuum inside the shell and also ensures proper circulation of heat transfer fluid in the jacket. The lump breaker within the dryer breaks large product lumps to powder form. The rotary action of dryer along with mechanical action of lump breakers reduce the drying time, deliver lump-free product and ensure extremely low moisture levels in the product.
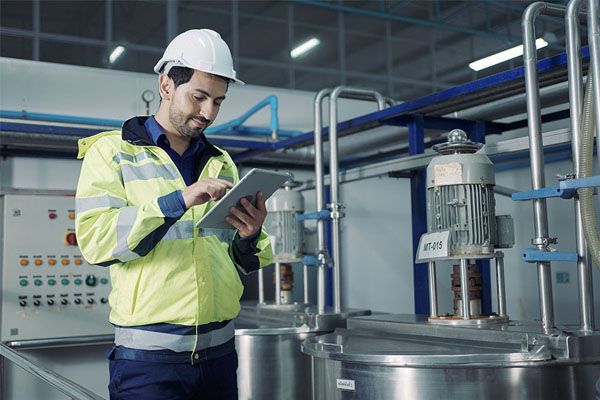