Process Reactors & Pressure Vessels
At the heart of every industrial process systems across industries are Process Reactors & Pressure Vessels. An industrial process reactor is an important chemical equipment that facilitates a wide range of processes such as optimal mixing, flow distribution, heat transfer, mass transfer, diffusion, etc. to deliver high-quality product. Industrial pressure vessels are containers for the containment of pressure either external or internal. The main purpose of a pressure vessel is to hold gases and liquids safely without placing any danger on the surrounding area.
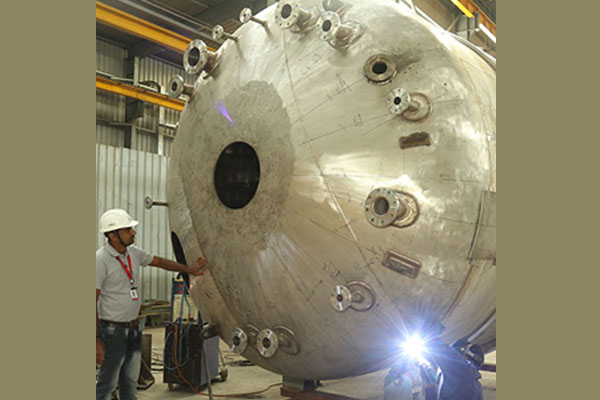
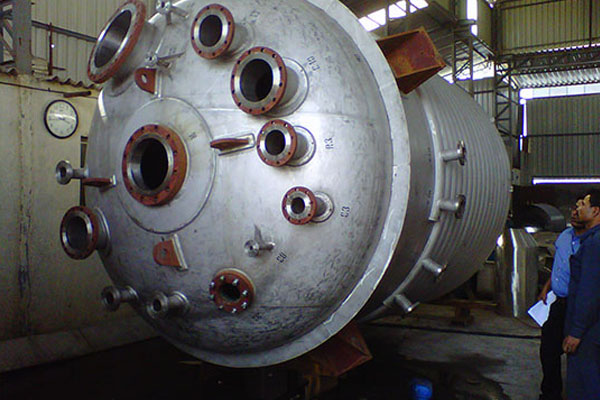
PROCESS REACTORS
Process reactor is a generic term used for equipment that carry out a variety of processes including hydrogenation, and processes that require critical equipment to create a process conducive environment for the reaction to occur at desired levels. Depending on the nature of reaction, a reactor may serve as a holding tank, heat exchanger, mixing tank or a mass transfer device. Chemical reaction generates desired product and by-products that can be used in downstream processes.
With proven expertise for adiabatic reactors, batch reactors, semi-batch reactors, continuous flow reactors, and more, ACME products have performed flawlessly delivering higher rate of desired output. Our team uses computational fluid dynamics (CFD) as a simulation tool for the development, design and optimization of processes. With the use of latest and advanced software, ACME has gained its expertise in designing the reactors as per ASME Sec VIII Div. I & PED 2014/68/EU.
ACME Engineers understand that a successful commercial unit is an economical balance of all the above mentioned factors, and designs reactors after considering every minute detail of the process requirement, also including: yield, purity, pollution, temperature, pH, oxygen and reactant concentration.
PROCESS REACTORS
Pressure vessels are containers for the containment of pressure either external or internal. A pressure vessel is designed to hold gases or liquids at a pressure substantially different from the gauge pressure. The pressure may be obtained from an external source, or by the application of heat from a direct or indirect source, or a combination of both. The main purpose of a pressure vessel is to hold gases and liquids safely without placing any danger on the surrounding area.
- Austenitic Steels – SS 304/304L, SS 316/316L, SS 321, SS 317/317L, SS 904L
- Duplex Steels – Duplex 2205, Duplex 2209,
- Carbon Steels – SA 516 Gr. 70, IS 2062,
- Exotic Materials such as – Hastelloy C-276, Hastelloy C-22, Titanium Gr. 2., Inconel 600, etc.
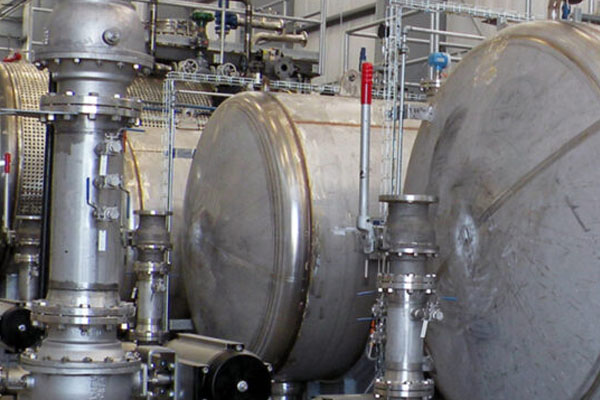
Ranging from 0.05 m3 to 100 m3, ACME has manufactured multiple capacity reactors and pressure vessels in various raw materials grades such as ACME designs & manufacture pressure vessels, jacketed vessels, limpet coil vessels, storage tanks and base frames, with ASME SECTION 8: Boiler and Pressure Vessel Code (BPVC), DIV 1 code- Rules for construction of process reactors and pressure vessels.
ACME have been certified by reputed inspection agencies such as TUV, Lloyds, BVIS, QUANTO, ELECTROMECH, SGS, DOSH and many more, for the quality of process reactors and pressure vessels. This makes us capable of delivering critical equipment for any project absolutely everywhere in the world.
APPLICATIONS
Catering to multiple process industries, ACME has developed its reactors to function efficiently in high pressure & high temperature applications, high corrosion resistance applications and Cryogenic applications.
- Fermentation of beverage products
- Waste water treatment
- Polymerization
- Brewing
- Oil cracking
- Petrochemical Products
- Fertilizer manufacturing
- Oxidation process
- Hydrogenation process
- Nitration process
- Synthesis of chemical intermediates
- Industrial Compressed Air Receiver
- Recompression Chambers
- Autoclaves
- Pneumatic and Hydraulic Reservoir
- storage Vessel for liquefied gases such as ammonia, chlorine, propane, butane, LPG, and more
- Storage and Pressurization Systems
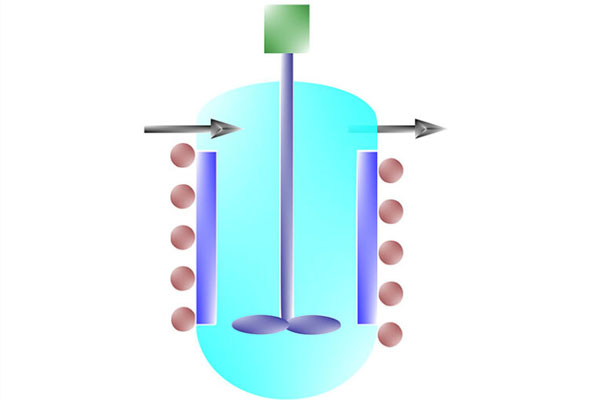
STRUCTURE OF A TYPICAL PROCESS REACTOR
- Reactor with process-specific MOC
- Process Specific Agitators
- Jacketed and coils for heat transfer
- Process Inlet / Outlet