Agitator For Mixing Hydrated Lime Slurry In Intermediate Bulk Tank
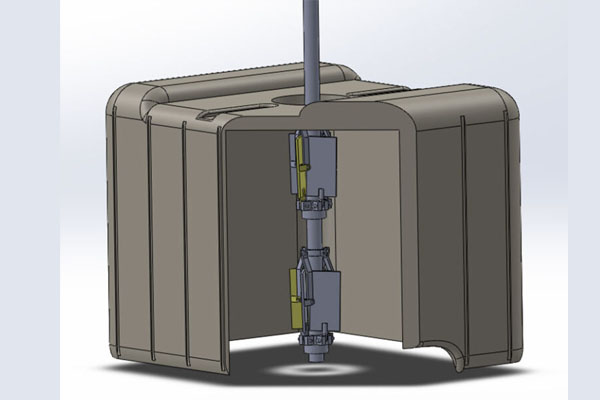
Intermediate Bulk Containers (IBCs) are generally used to handle, store and shipping of:
- Raw materials used in production processes
- Liquids and Solids (Granules or Powdered) food additives or ingredients
- Hazardous bulk chemicals.
- Petrochemical products such as oils, solvents, adhesives etc.
- Pharmaceutical components, intermediates, batch products
- Paints and industrial coatings
- Additives used in waste water, process water.
When these above material are stored in IBC's, there arises the need of homogenizing, suspending and dissolving contents in IBC containers before its use in the process since the materials stored could consists of two immiscible liquids or re-suspension of solids in heterogeneous mixture of solids and liquids, or mixing of additives to bulk liquid to form required product.
s
To select the effective agitator for given application the viscosity of material is the important physical property to be known. Number of Impeller types are available for selection for required application.
IBC Agitator For Mixing Hydrated Lime (Ca(OH)2) Slurry
Hydration conditions of the Lime slurry changes its viscosity. Variations of viscosity of hydrated lime slurry have been derived between the range of 40-80 Kerbs unit. Improper mixing of Hydrated lime in IBC tank the solid particles agglomerates causing settling of particles out of slurry at the bottom and corners of the IBC, which results in less viscous slurry than the desired for the application and gets less yield of desired Lime slurry as the settled particles remain in the tank after draining the slurry obtained from improper mixing.
This problem can be resolved by Proper agitator design and process understanding. Selecting a small or inappropriate impeller is the most common mistake because it introduces irregular axial flow patterns which leads to stratification of fluid and settling of solid particle which is observed mostly in corners of tank and required cleaning if solidified.
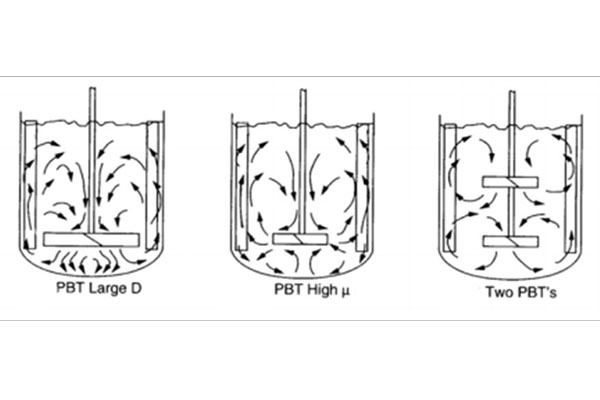
Figure 1: Liquid flow patter for Pitch Blade Turbine impeller with large Diameter, high Viscosity, and multiple impellers
It is recommended that aggressive agitation speed and impeller type are suitable for these type of application because the types of slurry that settle are not shear sensitive. The most appropriate impeller for these type of slurries are 4-bladed 45° pitched turbines which can handle a variety of mixing services.
Appropriate mixer selections must be made dependent on process optimization and solid-liquid physical properties as agitators and impellers of same size does not fits to all applications.
The selection of suitable agitator for hydrated lime slurry in IBC tank was done on basis of a balance in Number of blades, Number of impellers, power consumption, RPM, shear rate, vessel and vessel inlet geometry and the lab trials. All the above factors determined the best agitator for the maximum quality control.
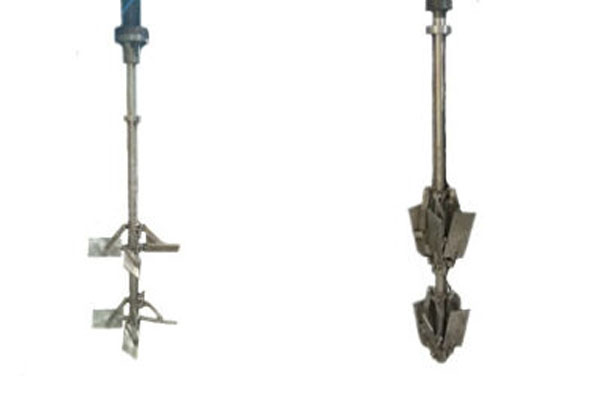
a) Open Position b) Close position (upside folded)
ACME's Upside Foldable 2 Impeller - 4 Bladed PBT Agitator
At ACME we have developed Upside Foldable 2 Impeller – 4 Bladed PBT Agitator for 1KL IBC tank for effective and controlled mixing of Hydrated Lime (Ca(OH)2) Slurry in it. It ensures the complete mixing in IBC and prevents solids from settling down at the bottom. The agitator is top entry agitator with designed motor and gearbox.
The impellers will be in close position while entering through the small opening of the IBC tank top and will unfold in the tank before mixing starts. When agitator has to be removed from the IBC tank the impellers blade are folded upside so that they can be easily taken out of the tank opening without disassembling the agitator components like motor, gearbox and shaft.
At ACME we have developed Upside Foldable 2 Impeller – 4 Bladed PBT Agitator for 1KL IBC tank for effective and controlled mixing of Hydrated Lime (Ca(OH)2) Slurry in it. It ensures the complete mixing in IBC and prevents solids from settling down at the bottom. The agitator is top entry agitator with designed motor and gearbox. The impellers will be in close position while entering through the small opening of the IBC tank top and will unfold in the tank before mixing starts. When agitator has to be removed from the IBC tank the impellers blade are folded upside so that they can be easily taken out of the tank opening without disassembling the agitator components like motor, gearbox and shaft..
Specifications
- Impeller sweep diameter open position : 550 mm
- Impeller seep diameter close position: 190 mm
- No. of Impellers: 2 Nos
- Shaft Diameter: 50 mm
- Shaft length: 1450 mm
- MOC: SS 316
- Motor: 5.5 KW/4 pole/50Hz/420V/VFD suitable
- Gearbox: Inline helical/ Reduction Ratio: 1:8
- Optimum Operating RPM: 130-140
- Operating time: 15 min
- Current Load: 6 Amps
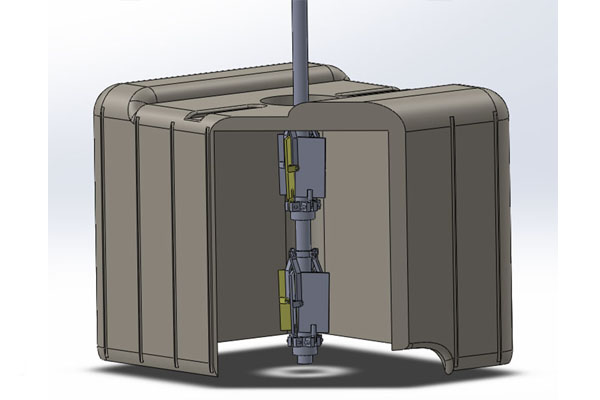
a) Open Position in IBC tank
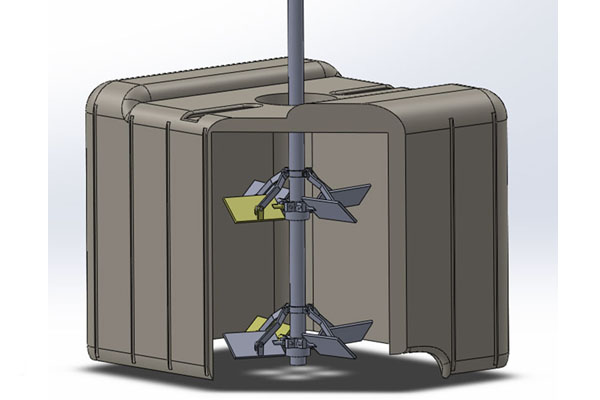
b) Close position (upside folded) in IBC tank
Advantages
- High viscous slurries can be effectively mixed without settling or accumulation of solid particles.
- High shear mixing.
- Sweep diameter of impeller can be increased.
- Operates at low RPM 100-150 RPM.
- Due to upside folding the clearance between tank bottom and agitator can be reduced up to desired limit.
- Same agitator can be used for mixing in multiple IBCs.
- Reduces IBC tank cleaning intervals and gives maximum yield.
- Short mixing time.